製造業の生産管理をしていて、ライントラブル・現場作業者の能力不足やミスにより納期遅延・納期調整が発生してはいませんか。
そして、トラブル対策を求められているけれど、毎回起きるトラブルの事象が異なるため対処方法に手間取ってはいないでしょうか。
- 起きたライントラブルに対して適切な対応が取りたい
- 対処する優先順位をつけられるようになりたい
- 対策を打てるようになりたい
このような生産管理担当者に向けて、品質管理に欠かせない「4M」ついて徹底解説します。
本記事を読めば、 トラブルの発生要因分析からトラブル発生直後の対応方法、優先順位付けができるようになります。
また、体験事例を紹介していますので実務に生かしてください。
目次
4Mとは
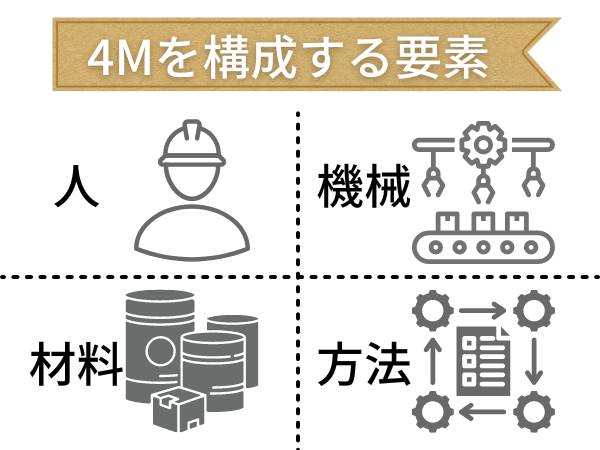
4Mとは、Man(人)/Machine(機械)/Material(材料)/Method(方法)の4つの要素を表します。この4つがうまく機能して良品を製造できるのです。
4つ要素がどのような機能を持っているのか、それぞれの項目について詳しく解説していきましょう。
人(Man)
4つの要素で最も重要なのは、現場作業員(人)です。
良品を継続的に製造するには、現場作業員の技能を維持しなければなりません。製造現場を見ていただければわかる通り、機械操作や原材料の配合、加工技術など現場作業員の熟練したスキルによって製造現場が成り立っています。
近年では、作業員がロボットへ代わっていますが、ロボットを操作するのは現場作業員の仕事です。業務がロボット操作に置き換わっても、製造ラインについて詳しい方がいればトラブル発生時は適切に対処できます。
そのため、4Mの重要要素である作業員(人)は、技能や経験に基づいて人員配置されている必要があるのです。
ただし、配置を長期間固定するとスキルの伝承ができなくなるため、定期的な配置換えは必要でしょう。
機械(Machine)
4Mの2つ目の要素は機械です。製造ラインには製品製造のために必要な機械が用意されています。良品を効率よく製造するには、以下について考えなければなりません。
- 製品の流れに合う最短・効率のいい設備レイアウトになっているか
- 点検をして消耗品の交換はされているか
- 古い機械を新しい機械に入れ替えているか
特に、点検や消耗品の交換を怠ると不良率が高くなるので、定期的なメンテナンスが必要です。
また、「古い機械を新しい機械に入れ替えているか」については、一般家庭の話に置き換えると車に例えられます。
つまり、技術は進歩して燃費のいい車が売られているのに、古い車に乗り続け、高い税金とガソリン代を払っているのと同じなのです。
材料(Material)
4Mの3つ目の要素は材料です。製品の製造には原材料や部品が必要となります。
この原材料や部品が以下のように管理されて、質の高い製品をコストパフォーマンス良く製造ができるのです。
- 適正な在庫量であるか
- 適正な受入検査をしているか
- 最適な仕入先/仕入価格/運送方法か
後半では、4Mの不十分な材料管理で起きた不良品流出の体験事例を紹介するので参考にしてください。
方法(Method)
4M最後の要素は、方法です。製造ラインをうまく動かすためには、各作業の業務標準書が必要です。
また、「決められた手順」「決められた方法」で作業しているか定期的に確認が必要です。もし、業務標準書通りに作業しているにもかかわらず、不具合が出たのであれば原因を特定して見直さなければなりません。
「5M+1E」「6M」という品質管理における新要素
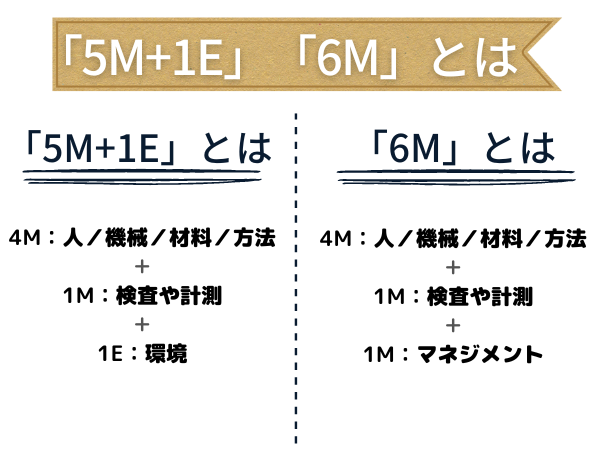
「5M+1E」とは、4Mに「検査・計測(Measurement)」と「環境(Environment)」が加わったものです。
もともと検査・計測は、4Mの「人」「機械」「方法」に含まれている要素だったのですが、不良品流出を防ぐには検査や計測が不可欠という考えのもと、5つ目のMが設定されました。
なお、検査・計測では以下の要素が正しく機能して、安定した計測値が出ます。
- 熟練した検査・計測者
- 設定・メンテナンスされた計測機械の使用
- 正しい計測方法
そして、材料によっては温度や湿度で形状が変わってしまうものがあるため、環境の管理が必要とされるようになり、Environment (環境)の1Eが生まれました。
また、6Mとは上記「人」「機械」「材料」「方法」「検査・計測」の5Mに「マネジメント(Management)」を加えたもの。
マネジメントが加えられた理由は、多品種少量生産のニーズに対応するためです。
多品種少量生産は短期間に製造ラインや作業内容の変更が必要になるため、製造中の製品に合った設定になっているかのマネジメントが必要です。
4M分析|4Mで起きるトラブルの原因を徹底解説
ここでは、製造現場の4Mで起きるトラブル内容と発生要因の分析方法を紹介します。
起きたトラブルを解消するだけでは今後のトラブルは防げません。トラブル内容から発生要因を分析し、今後の対策につなげましょう。
それでは、4Mで起きるトラブル内容を解説します。
4Mで起きるトラブル:人(Man)
人によるトラブルは、主に2点あります。
1点目は現場の配置転換による予期せぬ作業ミスです。特に初めての作業はミスをする可能性が高まるため、マニュアルが必要です。
そして2点目は、作業内容の変更による作業ミスです。設計変更があった際は、「図面が変わった」「加工寸法が変わった」など、詳しく情報共有をして作業内容の確認を行います。
4Mで起きるトラブル:機械(Machine)
機械によるトラブルは、3点です。
1点目は、消耗品の交換がされていなかった場合です。
もし、旋盤の刃などの消耗品が交換されていなければ、加工が不十分だったり作業時間がかかったりします。そのため、機械の点検・消耗品交換はトラブルを防ぐために必要です。
なお、点検や消耗品交換のタイミングは機械動作数値の記録で判断できるので、日々記録して正常値と異常値を確かめましょう。
機械による2点目のトラブルは、新しい機械を導入した時です。
新しい機械への登録情報が間違っていれば不良品を生み出してしまいます。そのため、新しい機械の導入時は必ず試作・検査をしましょう。
そして3点目は、「作業する製品」と「機械に設定した情報」が合っていない場合です。
機械に設定した情報が他製品のものだった場合、当たり前ですが、不良品を生み出してしまいます。
自動の加工機を例にすると分かりやすいでしょう。製品を設置し、ボタンを押すと自動で加工されますが、設定情報が間違っていれば不良品を大量発生させてしまいます。
そのため、これから作業をする製品と機械に設定した情報が合っているか確かめましょう。
4Mで起きるトラブル:材料(Material)
材料が原因で起きるトラブルは大きく3点あります。
1点目は現場で起きる材料の配合ミスです。これは、作業マニュアルや作業ワンポイントで防ぐことができます。
材料が原因で起きるトラブルの2点目は、材料を変更した時です。
同じ材料名であってもメーカーによって配合が異なるため、以前と同じ品質で作れなくなるのです。
そして3点目は、原材料や部品の在庫管理不足による在庫切れです。
4Mの「材料」の中でも、原材料や部品の在庫切れは起こる確率の高いトラブルではないでしょうか。
実は、原材料や部品の在庫切れは、在庫管理不足はシステムで解決できます。後述していますので、ぜひ最後までお読みください。
4Mで起きるトラブル:方法(Method)
次に、方法が原因で起きるトラブルは複数あります。
「管理方法」「検査方法」「伝達方法」など、4Mの要素である「方法」は主に、準備不足や情報伝達ミスによりトラブルが起きています。
例えば、作業方法の変更があった場合、情報共有漏れは確実に誤作を発生させます。
そのため、作業変更内容を朝礼やミーティングでの情報共有が必要です。
特に常勤・1勤・2勤と作業者が複数グループに分かれる場合は情報共有をしましょう。
なお、製造業において、図面の変更時は最新版管理を徹底し、改訂履歴も分かるようにします。
製造業におけるトラブル発生要因の分析方法
生産管理の仕事をしていると、あらゆるトラブルに見舞われることがあるでしょう。トラブルの発生場所や要因がさまざまあると状況整理がしにくくなるのです。
そこで、誰もがトラブル発生要因の分析ができる「特性要因図」の書き方を紹介します。
特性要因図では、発生要因を4Mの要素に仕分けし、「トラブルの内容」と「思い当たる要因」を書き出していきます。それでは順に解説していきましょう。
- 紙に→(右矢印)を書いてください。
- 4M(人・機械・材料・方法)を上下に2つずつ書きましょう。※下記画像の黄緑色部分
- 4Mで起きたトラブル内容を記載します。※青文字部分
- 考えられるトラブル要因を書き出していきます。※赤文字部分
これで、どこの工程でどのようなトラブルが起こっているか可視化できました。
下記図を参考に、製造トラブルを可視化してみてください。
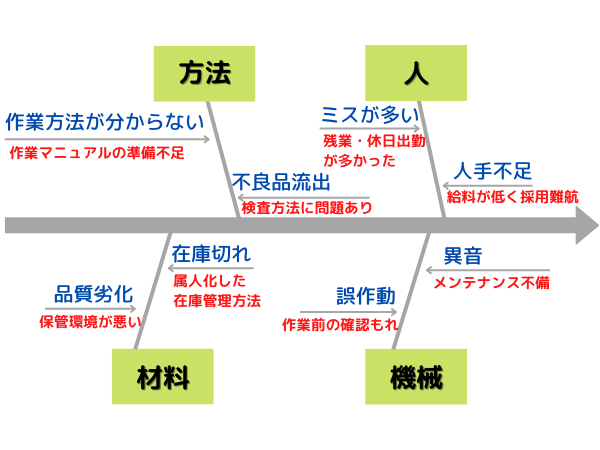
ぜひ、生産管理担当者と現場で情報を共有し、今後の対策を話し合ってみてください。
4M変更|トラブル解決後の変更点を管理する
トラブルを分析、解決したら変更した部分を文書として残します。変更点を記録する文書は、変更点が及ぼす作業の大きさによって変わります。「マニュアル」「管理表」「変更申請書」「作業報告ノート」など、会社や現場によってさまざまです。
作業変更点を文書として残す理由は、変更点が原因で不具合が起こったのか特定するためです。
また、文書として残しておけば作業者同士の情報が共有しやすくなります。
なお、文章に残しておくべき4Mの変更点の具体例は以下です。
- 人:担当者の変更/休暇/勤務体制の変更
- 機械:情報変更/改造/移動/工具・治具の変更や更新
- 材料:原材料の変更/仕入先やメーカー変更
- 方法:製造条件や図面の変更/検査方法の変更
トラブル発生直後の適切な対応方法
トラブルが発生した直後は、顧客に迷惑をかけないようにリカバリを図らなければいけません。まずは、トラブルが数時間で解消される内容か、または数日かかるのか確認するために現場に行き、担当者に確かめましょう。
次に、「影響を受ける可能性のある製品」のデータ抽出を行います。影響を受ける可能性のある製品とは、仕掛品やこれから生産予定の製品です。
仕掛品と生産予定製品の「在庫数」「受注数」「納期」のデータを作り、全体を把握しましょう。そして、優先順位を付けていきます。
なお、優先順位をつけるときはグループ分けすると分かりやすいです。
急ぎ(大):在庫なし/受注あり/短納期
急ぎ(中):在庫なし/受注あり/納期は余裕あり
急ぎ(小):在庫少/受注あり/納期は余裕あり
※現場へ指示する納期は、明確に「工場出荷●月●日」と明記しましょう。
また、効率よく製造ラインを回すには治具や加工データ、部品の組み立てなど、同じものをまとめるのも1つの方法です。
最後に、優先順位の製品を納期通りに進めるには「残業」「休日出勤」「一時的な増員」「代替設備での対応」など対応方法を即座に決めなければなりません。
「製品を発注・統括している部署」と「生産現場を統括する生産管理の部署」が話し合い、必要な対応を取ります。
トラブル解決の優先順位付け方法
トラブルや課題が複数ある場合、何から解決したらいいか分からない時があるでしょう。
何から手を付ければいいか分からない状況になったら、「トラブルや課題が与える損失の大きさ」を想定して、損失の大きい順に解決していきます。
製造業において品質面に不具合が出ると、最も損失が大きくなるため、社外へ影響を及ぼす内容は最優先の解決事項です。
もし、社内でリカバリを図れる内容であれば優先順位を下げても問題ありません。
しかし、リカバリで対応できるからといってトラブル要因を解決しないのは問題です。
現場作業員はトラブルを発生させないよう、常に気配りをしながら業務に当たっているため、トラブル要因は放置せず、必ず解決させましょう。
ずさんな4M管理で起きた体験事例と学んだこと
ここでは、ずさんな4M管理をしていたために起きた「部品の品質トラブル」について紹介します。
以下から体験事例です。
長年、外注していた部品に不良品が発生。気づかずに受け入れていました。
受入検査はしていましたが、長年お付き合いのある外注先だったため信頼し、簡易的な検査で済ませていたのです。
現場から「部品を製品へ組み付けているときに破損する」と報告があり品質トラブルが発覚しました。このとき、部品が基準の荷重に耐えられないと分かりました。
そこで、破損した部品在庫を即座に全数検査しました。全数検査時に不良部品のロット№を調べ、いつから不良品だったか把握しました。
また、「不良部品を組み付けた製品が顧客へ流出していないか」「物流にある製品の部品確認」が必要です。
さらに、同外注先から仕入れている他の部品も不良品でないか検査しなければなりません。
この期間、同外注先から仕入れた部品は組み付けられないため、対象製品の製造はストップしました。
営業窓口となる部署は納期調整や生産リカバリの調整に当たることになり、工場の品質管理課は3カ月ほどの残業と休日出勤をしました。
また、外注先の仕入れ部品は3カ月ほど抜き取り検査を実施しました。
そして、部品の全数検査終了後、外注先への是正措置と指導のために関係者が訪問。この訪問時に分かったのは、外注先で部品の資材変更がされていたことでした。
以上が品質トラブルの体験事例です。
この経験から学んだのは2点。
1点目は、外注先(仕入先)への定期的な訪問と検査が必要ということです。
今回紹介したトラブルは、資材変更をしたにもかかわらず当社に知らされなかったのが原因でした。しかし、そもそも仕入先へ訪問せず、関係が築けていなかったために出た悪い膿(うみ)だったのです。
長年の付き合いがあるからといって信頼しすぎてはいけません。受入検査の他にも、年1回は材質検査などの中規模な検査を行いましょう。
2点目は、トラブル時は不良品の流出を防ぐために、いかに早く、「部品の仕入れや在庫」「製品への組立状況把握」「製品の在庫データ」を用意できるかが重要ということ。
対応が後手にならないよう、在庫データを抽出し、データ加工できる能力は生産管理をする上では必須です。
改善の際は他部署の協力とシステム導入が有効
小さなトラブルに対する業務改善は自部署だけでも行えますが、多くの場合が他部署を巻き込みながら改善活動をしなければなりません。
例えば、急な設備メンテナンスや試運転で工程が止まる場合、生産管理担当者は営業部の窓口となる部署に連絡して対象製品の生産をストップさせる調整が出てきます。
納期に影響が出る場合は自部署だけで解決しようとせず、他部署と連携しながらより良く改善していきましょう。
また、生産管理担当者や現場作業員が使いこなせるシステムで仕事を進めるのも有効です。
今回ご紹介したトラブル事例では、「部品や製品の在庫データ」や「仕掛品のデータ」をいち早く作成しなければなりませんでした。
もし、手書きの在庫表で部品管理をしていたら3カ月ほどでは解決しなかったでしょう。
製造業において、在庫管理のシステム化をしておくと業務効率が上がるだけではありません。
トラブル発生時には会社としての対応方針を決める必要な情報の1つとなるため、現代では在庫のデータ化は必須です。
在庫管理システムでは最適な4M管理が可能
当社が取り扱う在庫管理システムでは、部品や材料などの入出庫管理、ロケーション検索ができます。
そのため、在庫管理システムに登録した部品や材料の不具合時には、いち早く在庫状況を把握できるのです。
不良品の流出やライントラブルは、「日々起こる小さなトラブルの対処」「4M変更」「変更後の状況管理」をすれば防げます。しかし、トラブルが慢性化していると、現場の危機感は薄れてしまうでしょう。
そのため、現場には慢性化したトラブルは異常事態と認識させ、対策を取りましょう。
そして、不良品の流出という最悪のケースに対応できるよう、いち早く現状をデータ化できるシステムを準備してはいかがでしょうか。
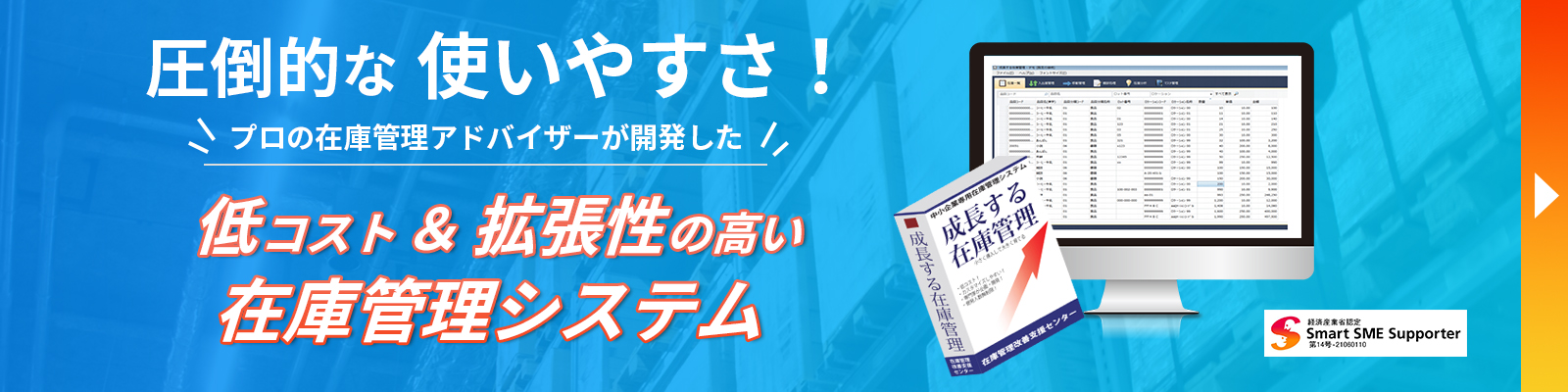
\ 在庫管理に関するお悩みは /