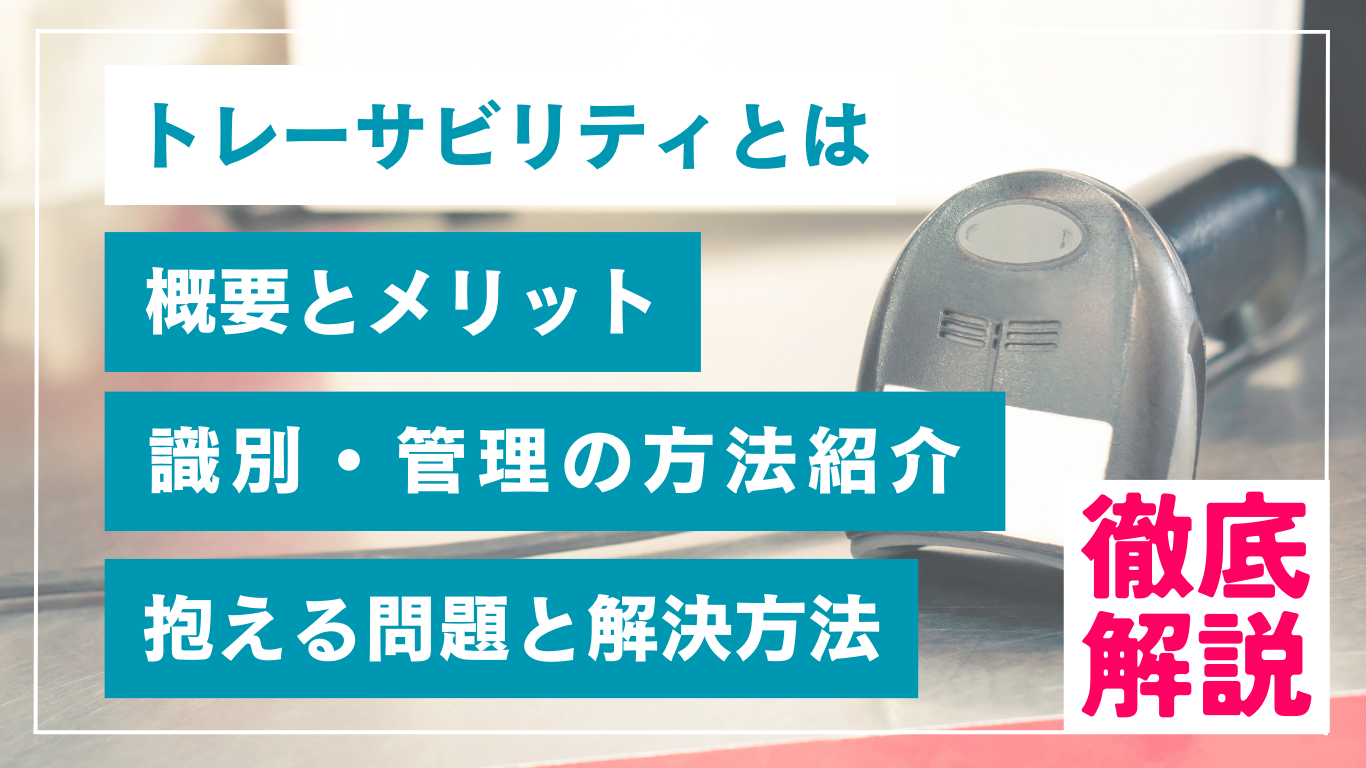
トレーサビリティは、製品の生産過程を追跡可能にし、品質管理や安全性確保を実現するための重要な仕組みです。品質管理部門、製造部門、開発部門の方は、トレーサビリティの知識を求められる場面があるかと思います。
本記事ではトレーサビリティの基本的な概念から、具体的な導入メリット、各部門で抱える問題とその解決方法などをわかりやすく解説しています。
より確かな製品品質を実現し、企業の信頼性を高めるためにトレーサビリティがどのように活用できるのか専門家が詳しく解説します。
目次
トレーサビリティとは、生産履歴を管理する仕組みのこと
トレーサビリティは生産履歴を管理する仕組み全体を指し、原材料から最終製品までの全ての工程をデータで可視化した状態をいいます。
トレーサビリティを整えることで品質管理や安全性の保証を実現させ、万一、トラブルが発生した時でも、迅速にその原因を特定し、適切な対策を講じることができます。
特に製造業においては社内での成型や加工、組み立てのみならず、外部から仕入れた原材料や部品、製品を顧客まで届ける物流に至るまで情報をさかのぼれる体制が必要です。そこで、トレーサビリティが有効となります。
トレーサビリティを活用した2種類の追跡方法
生産履歴をたどる方法として、「トレースフォワード」と「トレースバック」という2つの追跡方法があります。追跡方法を知り、トラブル発生時の解決手順として活用してください。
トレースフォワード
トレースフォワードとは、製品の生産過程を順に追跡することを指します。具体的には、原材料の仕入れから製品の製造、そして最終的に製品が顧客へ届くまでの全ての工程を順に追って追跡します。
トレースフォワードは製品リコール時に非常に役立ちます。例えば、ある製品に問題が見つかった場合、トレースフォワードを使ってその製品がどこへ出荷され、どの消費者が購入したかを特定できるからです。
また、トレースフォワードは、製品の流通経路を確認し、販売効率を分析するためのツールとしても活用可能です。
トレースバック
トレースバックとは、顧客が手に入れた製品から製造過程をさかのぼり、原材料まで戻って工程を追跡する方法です。トレースバックは品質問題や安全性の問題が発生した場合に、問題の原因を特定し、問題がどの工程で発生したのかを迅速に突き止めるのに有効な方法です。
トレーサビリティの種類
トレーサビリティにはサプライチェーン全体を追跡する「チェーントレーサビリティ」と、社内を追跡する「内部トレーサビリティ」の2種類があります。製造会社は、2つのトレーサビリティも整えることで生産過程に透明性が増し、顧客や取引先の信頼が得られるようになります。自社が強化すべきはチェーントレーサビリティか、もしくは内部トレーサビリティか、どちらなのか考えてみましょう。
チェーントレーサビリティ
チェーントレーサビリティとは、製品の1つひとつが特定の情報を持ち、その全ての情報がつながっている状態を指します。
具体的には、製品が原材料から製造、流通、販売という一連の流れの中で、どの段階でどのような処理が行われたのか、全ての情報がリンクされた状態です。製品に問題が発生した際、社内外のどこで問題が起きたのか原因を特定しやすくなります。
また、製品の在庫管理や配送ルートの最適化など製品の流通経路を把握し、運用の効率を向上させるのにも役立ちます。
内部トレーサビリティ
内部トレーサビリティとは、1つの組織や企業の中で製品の生産過程を追跡することを指します。
原材料の入手、製品の製造工程、製品完成までの各ステップを明らかにし、品質管理や安全性確保を実現します。
また、問題が発生した際には迅速な原因特定が可能です。内部トレーサビリティは自社内でどのように製造が行われたかを追跡する方法で、製造会社には必須ともいえるトレーサビリティです。
トレーサビリティの導入メリット
トレーサビリティの導入メリットとして下記が挙げられます。製造業の方にとってはどれも求めている内容でしょう。順に解説しますので、導入検討にご活用ください。
- 徹底した品質管理による安全性確保
- トラブル発生時の迅速な対応
- 顧客への情報提供による信頼獲得
徹底した品質管理による安全性確保
トレーサビリティを導入すると、製品の原材料から製品に至るまでの全ての工程を追跡が可能です。製品の品質が各工程で確保されているかを確認し、安全で高品質な製品を提供できるようになります。
トラブル発生時の迅速な対応
トレーサビリティを導入しておくと、問題が発生した際の迅速な対応が可能です。製品に問題が見つかった場合、どの工程で問題が起きたのかをすぐに特定でき、解決策を見つけ出せます。
もし、ある製品が顧客からのクレームを受けた場合であっても、どの原材料が問題を引き起こしたのか、または製造過程のどの部分に問題があったのかをすぐに調べられます。迅速な対応は顧客からの信頼性を保つのに重要な要素です。
顧客への情報提供による信頼獲得
トレーサビリティを導入することで、企業は製品の詳細な情報を顧客に提供できるようになります。消費者は製品の安全性や品質に対する信頼を深められ、企業にとっても自社製品の透明性を高めることにつながります。トレーサビリティには顧客の信頼を獲得し、ブランドイメージを向上させるメリットもあります。
トレーサビリティの導入デメリット
トレーサビリティはメリットが多い反面、企業には負担も生じます。ここでは、トレーサビリティを導入する際のデメリットを紹介します。
高い導入コスト
トレーサビリティを整えるには、専用のシステムを用意しなければなりません。ハードウェア、ソフトウェア、教育など、多くの初期投資が必要となるだけでなく、システムの維持・更新にも継続的なコストが発生します。専門業者に見積もりを取り、長期的にどれほどの予算が必要なのか算出しましょう。
複雑なシステム設計
製品の生産から流通までの全過程を追跡管理するため、システムの設計や運用が複雑になる場合があります。仕入から管理する場合は、システム設計がより複雑化するでしょう。
さらに、システムトラブルが起きる可能性はゼロではありません。迅速にトラブル解消ができるシステム会社なのかアフターフォロー等を事前に確認しておく必要があります。
膨大なデータを扱えるシステムの準備
追跡した大量のデータの保存が必要なため、適切なデータ管理とすぐに情報を取り出せるシステムが必要となります。データ保存だけでなく活用時の出力方法や出力可能数までも考え、システムを検討しましょう。
システムの統一
すでに他の組織が異なるシステムを利用している場合、1つのシステムでサプライチェーン全体の情報を共有できる体制を構築するには大変な労力がかかります。現状のシステムを活用しながら別のシステムを導入するか、新しいシステムで統一するか、コストと労力を考え検討しなければいけません。
同一品の区別
同じものを別物として区別しなければいけません。
そのため、現物に現品票を貼り付けたり、ロット番号を採番するなどして、区別できるようにします。
徹底したプライバシー管理
製品やサービスの追跡情報には、個人情報や企業の機密情報が含まれることがあります。これらの情報を保護するには、適切なセキュリティ対策とプライバシーポリシーを設置し、社内の徹底した管理が必要です。
トレーサビリティ3つの識別方法と2つ製品管理方法を紹介
製品がいつ、どこで、どのように作られたかの情報を得るには、製品自体に識別できるものが必要です。製品の識別方法を3つ紹介します。この識別方法を用いてどのように製品を管理すればよいのか、管理方法も解説しますので、ぜひ参考にしてください。
識別方法
製品がいつどのように作られたかを識別する方法として、レーザー印字、ラベル、RFタグの3つを紹介します。
- レーザー印字
- ラベル
- RFタグ
レーザー印字
レーザー印字とは、レーザーを用いて製品やパッケージに直接情報を印字する方法です。この印字方法は、製品の追跡情報や生産情報などを記録するために使用されます。レーザー印字は、耐久性が高く、摩耗や剥がれに強いため、製品寿命が長期であっても適切に追跡できます。また、高速で効率的な印字が可能であるため、大量生産においても対応できるのがメリットです。
ラベル
ラベルとは、製品やパッケージにバーコードやQRコードなど印刷されたシール等を貼り付けることで生産履歴を管理する方法です。ラベルは、製品の形状や素材に左右されにくく、また貼り付ける位置を選べるため、製品の種類によってはレーザー印字よりも適しているケースがあります。
RFタグ
RFタグとは、無線周波数を利用して製品に情報を埋め込む方法です。製品の追跡情報や生産情報などが記録され、読み取り機で情報を読み取ることができます。RFタグは、バーコードやQRコードと異なり、直接見える範囲でなくても情報を読み取れるため、製品の管理をより効率的に行えます。
製品管理方法
上記で紹介した識別方法を用いて製品を管理しようとした際、「シリアル番号」と「ロット番号」の2種類の管理方法のどちらかを使用することとなります。製品の特長に合わせて管理方法を選びましょう。
- シリアル番号
- ロット番号
順に解説します。
シリアル番号
シリアル番号は、製品や部品を1つひとつ識別するための番号です。
各製品に固有のシリアル番号を割り当てることで、製品1つひとつの追跡や管理が容易になります。高価な製品や、保証・修理対応が必要な製品に用いられることが多く、生産履歴や出荷履歴、保証情報などを確認する際に役立ちます。
ロット番号
ロット番号は、一定の生産ロットや生産期間に割り当てられる番号です。
一度に生産される製品ロットに同じ番号を割り当てることで、製品ロットごとの追跡や品質管理が可能となります。
万一、特定の生産ロットに問題が発生し製品リコールが必要となった場合、ロット番号で一括して追跡・対応できるため、迅速な対応にあたれます。
シリアル番号は個々の製品の追跡を、ロット番号は生産ロットごとに一括の追跡を可能とするため製品によって使い分けましょう。
各部門が抱えるトレーサビリティの問題とその解決方法
ここでは製造にかかわる各部門が抱えるトレーサビリティの問題と解決方法について解説します。
品質管理部門
【問題】品質情報が散在していて一元管理が難しい、情報の蓄積がうまくいっていない。
【解決方法】情報を一元管理できる管理ツールの導入をおすすめします。 事務所と現場それぞれで品質情報を管理していると、もし情報に齟齬があった場合、トラブル発生時に適切なデータの抽出ができません。まずは散在した情報の収集、情報の精査を行い、管理ツールに蓄積していきましょう。品質情報の散在を放っておくと、統一するのがさらに複雑になるため、早急の対応が必須です。
【問題】適切な品質基準の設定があいまいになっており、品質基準が順守されているかの確認が難しい。
【解決方法】製品の品質基準を明確に文書化し、全員が可視化できるようにします。そして、抜き取り検査を行い、検査結果を蓄積していきます。抜き取り検査は実施日と対象製品をあらかじめ決めておくことで製品をまんべんなく品質管理を行えるようになります。数値が安定しない事象が出てきたら、設備の老朽化や摩耗といった異変が起きている可能性があるため、早めに設備点検を行いましょう。
【問題】不具合製品の原因追及が難しい。
【解決方法】不具合が発生した製品の詳細な検査を行い、図面や各基準書に従って作られているかを確認します。不具合が発生した製品と同じ生産ロットや近しいシリアル番号の製品を調査し、他製品に不具合が生じていないか確認しましょう。そして、生産工程や品質管理プロセス、設備を見直し、問題が発生しうるポイントを特定します。
他にも、関連する部品や材料の供給元を調査し、問題が供給元から来ていないか確認することも必要です。
製造部門
【問題】データ入力の誤りやモレが発生し、生産情報の正確な記録・管理ができない。
【解決方法】データ入力の自動化や、エラーチェック機能を持つシステムを導入しましょう。担当者不在による業務停止が起きないよう、作業マニュアルを作っておくことも必要です。
【問題】生産工程が複雑で追跡が難しい。
【解決方法】QRコードやRFタグを用いて、製品の生産工程を追跡できるようにするのがおすすめです。例えば、加工委託が必要な場合、委託先の受け入れ可能数に応じて出荷先を決める場合があるでしょう。この場合、同じ製品であっても加工委託先が異なるため生産履歴も変わります。こうした生産工程が状況によって変化する際はQR コードやRFタグで「どこの加工先から戻ってきたか」を情報追加することで管理できるようになります。
【問題】部品の出所を特定しにくい。
【解決方法】部品供給元の情報をデータベース化し、部品の出所を特定しやすくします。受入日、部品番号、部品名、数量、ロケーション番号等の仕入情報と使用した履歴を管理する出荷情報をデータベース化しておくと出所を特定しやすいです。 複数の供給先がある場合、供給先(製造先)固有の識別番号を用意したり、供給先ごとに部品の保管場所を変えたりすることで、「いつ・どこから仕入れた部品を使ったか」特定しやすくなります。データと現物が紐付けられる体制を整えるのがポイントです。
開発部門
【問題】設計変更の履歴管理ができておらず経緯が把握しにくい。
【解決方法】設計変更の日付、変更場所、理由、図番といった履歴をデータベース化します。データベース化の際は図面と整合性が取れるよう、図番をキーに管理しておくことが重要です。
【問題】製品開発情報の共有が不十分で、透明性に欠ける。
【解決方法】情報共有ツールを導入し、開発情報の可視化を目指しましょう。閲覧権限を設定すれば、情報漏洩対策も可能です。
【問題】プロジェクト全体の進捗状況が把握しにくい。
【解決方法】状況が刻々と変わるプロジェクトは、他部署と足並みをそろえて進行していく必要があります。進捗状況の把握や情報共有に便利なのがプロジェクト管理ツールです。ガントチャート作成やタスク管理が可能で、誰がどのようなタスクを抱えているか可視化できるのが利点です。
トレーサビリティは原材料から製品に至るまで、もしくは製品が顧客の手に届くまでの履歴を追跡できる仕組みです。
トレーサビリティの導入により品質管理、安全性確保、問題発生時の責任追及が容易になります。
しかし、トレーサビリティを実現する生産管理システムの導入には多額の初期投資が必要です。
生産管理システムと連携可能な在庫管理システムでトレーサビリティを整えよう
成長する在庫管理システムは、標準でロット管理も可能です。
カスタマイズで、ロット番号の自動採番や、今回紹介したようなトレース機能(どのロットの原材料から製品を作ったか)も可能です。
「複雑な製品は作っていないから入出庫管理や部品表の作成ができれば十分」といった方には、生産管理システムよりも在庫管理システムの導入をおすすめします。
当社の在庫管理システムは、ロット管理機能やトレーサビリティ機能を追加でき、現場に合わせたシステム開発を強みにしています。 30日間使える無料お試し(基本機能のみ)もありますので、ぜひお試しください。
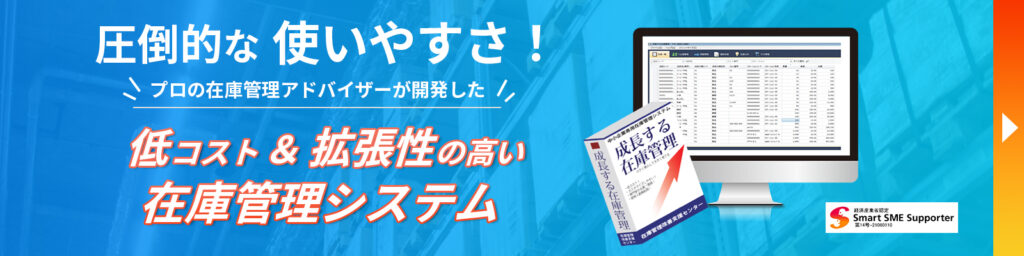