製造業において、生産性を改善するために現場のIoT化が進んでいます。
現実問題として、生産性を定量的に管理することは簡単なことではありません。しかしIoT化によって、「設備・製品・作業者」の情報を手間なく簡単に取得して、製造状況を把握できるようになります。
今回は、生産状況を改善する指標となる可動率に注目をしてみました。可動率を活かすことで、生産性の改善を実現することができます。
生産担当者であれば知っておくべき可動率の基本、システムの構築方法について解説をします。
目次
製造現場で生産状況を把握するのは困難
製造現場では日々、生産性の改善活動を行っていると思いますが、生産性を定量的に管理することは難しいものです。
現場にてサイクルタイムを取得しようとストップウォッチを持ち、現在の生産状況を取得しに行ったとしても限られた場所・限られた時間のサンプルでしかなく、そのデータの信頼性は低いのではないでしょうか。
ましてや、人・設備・製品毎(仕様毎)に作業時間は変動しますので、すべてを常に管理するのは非現実的です。
そのような“生産性を定量的に把握できない”課題を解決する手法として可動率システムが存在します。工場・設備のIoT化には欠かせない考え方です。
そこで今回は、可動率の基礎を学んでいきましょう。さあに可動率のシステム化についても、ご提案してまいります。
「可動率」とは
混同しやすい言葉で「稼働率」(かどうりつ)があります。
稼働率とは、機械や設備などの生産能力を100%としたときにどのくらい生産できたかを示す指標のことです。例えば、 1日1000個作れる設備で900個作った場合は、稼働率は90%です。逆に120個作った場合は稼働率は120%となります。稼働率を追う生産は、ムダの中で一番避けなければいけない「作りすぎのムダ」を生みます。
今回説明する可動率は「べきどうりつ」と呼びます。
可動率は「動くべき時間にどれだけ動いたかの比率」となります。言い換えると、「基準時間(動くべき時間)に対しての実績時間(どれだけ動いたか)の比率」となります。 つまり、可動率は、「達成すべき生産高」で、100%を目指さなければいけません。
簡単な例を上げます。ある製品を組立する工程があったと仮定します。
その製品を組み立てる基準時間(理想値)が80秒と決めていたとしましょう。
その製品を組み立てる実績時間が84秒であった場合、80秒(基準時間)/84秒(実績時間)=95.24%となり、可動率は95.24%となります。
つまり、4秒は可動ロス時間となります。
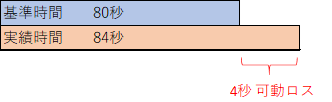
これは1サイクルでの説明ですが、実際の現場では連続して組立を行います。
その場合、すべての組立時間を合算して可動率を算出します。
下図の場合、基準時間80秒✕8個=640秒が組立全体における基準時間となります。
640秒(基準時間)/680秒(実績時間)=94.12%。
つまり、94.12%が可動率となります。
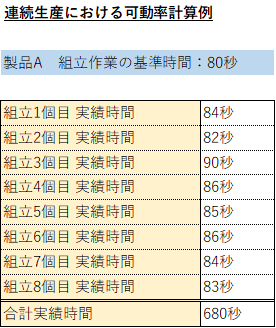
※可動率の定義について補足
本記事では可動率の定義を「製品を製造する過程で、人・設備が動くべき時間(理想値)にどれだけ動いたか(実績値)」の比率と定義します。
可動率をインターネットで検索すると「設備が動くべき時間にどれだけ動いたか」の指標として用いられる説明が多いですが、本記事では設備に限らす、人・製品(製造方法) も含めて、生産性の指標として可動率を表現してまいります。
このあたりの式や対象の定義は、可動率を用いている会社によって違う場合があります。
共通していることは、「生産性・稼働状況に関わる指標を指す比率であること」です。
IoT化における「可動率」の活用方法
この記事で紹介する可動率はさまざまな活用方法が存在します。以下では、IoT化によって取得できる情報を活かして、生産性が改善できるアプローチ手法を紹介します。
(1)生産性の指標(IoT情報の活用)
可動率は単純な設備の生産稼働性の指標だけでなく、他の情報と組み合わせることで様々な生産性の指標となります。
他の情報とは、IoTの基本となる情報である、”設備”,”製品”,”作業者”の情報です。
IoT情報を組み合わせることで、“設備毎の可動率”,”製品毎の可動率”,”作業者毎の可動率”の見える化が可能となります。もちろん、設備と作業者を組み合わせた可動率も算出可能です。
具体的に可動率を見える化したイメージ図を示します。
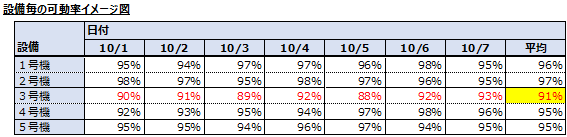
設備毎で見たとき、3号機の可動率が他と比較して低いですね。
この場合、3号機に何らかの問題があることが考えられます。
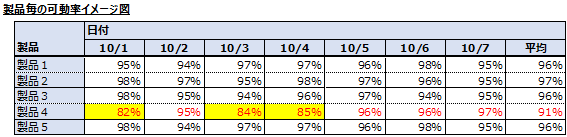
製品毎で見たとき、製品4の可動率にバラツキがあるように見えます。
この場合、特定設備 もしくは 特定作業者で生産したときに、可動率が低くなる原因が潜んでいるのかもしれません。詳細調査する価値があることが読み取れます。
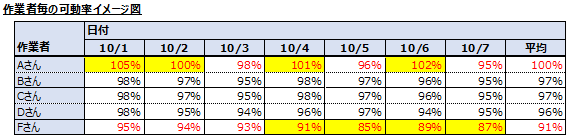
作業者毎で見たとき、Aさんの可動率が100%を超過しています。この場合、基準時間の設定が誤っていることが考えられます。
又 Fさんの可動率が減少傾向です。何らかの問題が生じていることが考えられますのでヒアリングして、原因を聞き出してみるのも手かもしれません。
このようにIoT情報を活かしながら、様々な角度から可動率を見ることで生産性改善のヒントを作ることができますし、改善策を行った後の効果確認にも活用できます。
今回の例では特定の項目に絞っての可動率でしたが、現場のIoT化では設備・製品・作業者を掛け合わせた可動率を参照することが一般的です。
(2)チョコ停・ドカ停の見える化
普段の生産性はもちろんですが、チョコ停/ドカ停など現場から管理部門に上がってこないような情報も見える化が可能となります。
下表のような状況があったと仮定します。
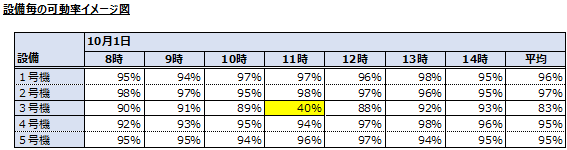
3号機にて11時台に可動率が大きく低下していることが分かります。このタイミングで何らかの障害が発生したと考えられるのです。
ここから、現場ヒアリング 及び 設備のアラーム状況を調査を実施し、何が原因でこのような状況が発生したかを原因追求し、安定的な生産性を確保できるよう対策を行うことができます。
可動率を算出するうえで必要な情報
可動率を算出するうえで必要なのが、単純なサイクルタイムの情報だけでなく非稼働時間の管理がポイントとなります。非稼働時間とは昼休み中や定期メンテナンス中、毎朝の点検作業など、本来稼働すべきでない時間のことを指します。
この非稼働時間のことをNOT(Non Operation time)やNWT(Non-Working Time)と呼んだりする場合もあります。
この非稼働時間を、いかに検知するかがポイントです。
一番簡単な方法は設備備え付けのタッチパネルや設備付属のコンピュータで、“生産開始”/“生産終了”といった情報を入力してから、設備を稼働可能とする案です。
こうすることで、漏れなく生産の実態を管理することが可能となります。
また、製品を製造するうえで、多くの現場で発生する製造製品の変更による段取り作業です。この段取り作業についても、基準時間と設け、実績時間を収集することで段取り作業の可動率を算出することが可能となります。
では、とある設備の1時間の稼働状況を図にしたものを見てみましょう。
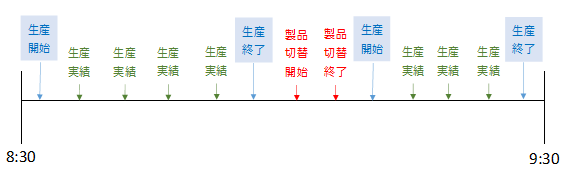
それぞれのデータが発生した瞬間の時刻を用いて、各時間の内訳時間を決めていきます。
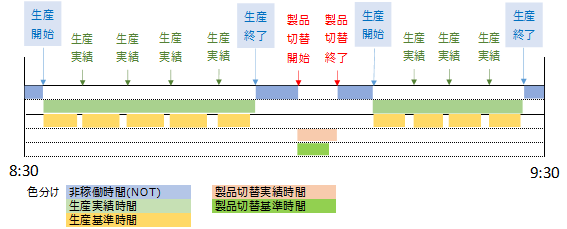
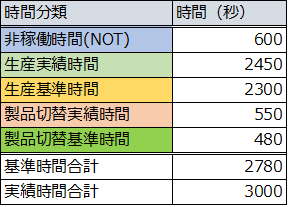
これらの時間の内訳を集計した結果が上表の通りだった場合、可動率は2780秒÷3000秒=92.67%となります。
このように基準対実績を用いた管理を行うことで、現場の生産性を定量化することが可能となります。
可動率システムの構築方法例
ここまでは、「可動率とは何か」および、IoT情報を使った「可動率の活用方法」についてご紹介してまいりました。
ではここで、どのようにしてこのシステムを構築するかについて解説してまいります。
実際のシステム構築については、各生産現場によって違ってきます。ですが、基本的な考え方については同様ですので、ご参考に頂ければ幸いです。
(1)設備/現場のIoT化
現場のIoT化は必須の条件となります。
具体的には下記イベント情報が最低限必須となります。
・生産開始情報
・生産終了情報
・生産実績情報
また、これらの情報に “誰が”、“どの設備・場所で”、“何を”、“どのように(どのレシペ/どのプロセス)”といった情報を付与することで、“詳細な現場の実態“を把握することが可能です。
その他、下記の情報も送信できると、より柔軟な時間の管理が可能となってきます。
・定期補修情報
・確認作業情報
・休憩情報
・切り替え作業(前段取り/後段取り)
設備や製法によって、これらの情報を効率的に取得する方法が変わってきます。
工場の従業員一丸となってアイデア出しを行い、IoT化をご検討してみてはいかがでしょうか。
相談等ございましたら、ご気軽にお問い合わせ下さい。
(2)各作業の基準時間設定
定型的な作業については、基準時間を決めます。
基準時間については、理想の最短の時間を設定することがポイントです。
生産実績にはもちろん基準時間を設定しますが、定期補修情報/確認作業/切り替え作業についても基準時間を設定することで、より詳細な可動率の表示が可能となります。
また、生産実績の基準時間が一番の重要なポイントとなってきますが、基準時間の設定は“生産設備種類(型式)”及び“製造品”毎の設定をできるようにしておけば、より精度の高い基準時間設定が可能となってきます。
そうすることで、異なる拠点間、同一設備・同一製品の可動率比較が可能となってきます。
結果、拠点間での作業方法のバラツキの検知が可能となってきます。
(3)可動率の算出
先ほど図で説明した内容を使って、可動率を算出してみます。
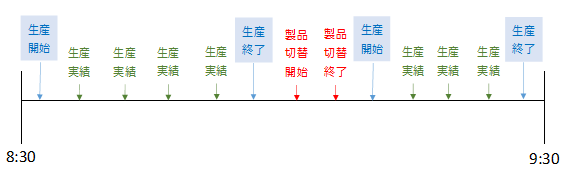
A.IoTで取得した内容をもちいて、設備毎にイベントを時系列に並べます。
B.時間を分類し、分類毎に時間を集計します。これで実績時間の集計完了です。
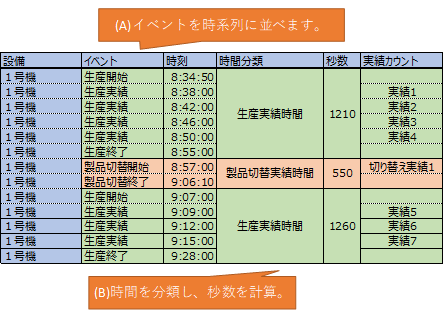
C.各実績をカウントし、それぞれの基準時間を設けます。
例)1生産の生産実績基準時間=300秒
1製品切替の切替基準時間=480秒
生産実績数 ✕ 基準時間 = 生産実績基準時間
7回 ✕ 300秒 = 2100秒
製品切替実績数 ✕ 基準時間 = 製品切替基準時間
1回 ✕ 480秒 = 480秒
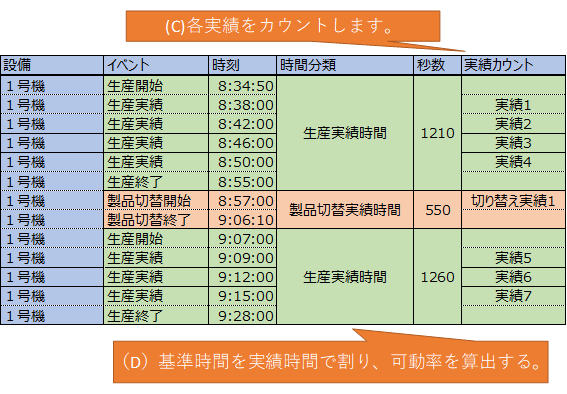
D.これまでで求めた基準時間と実績時間を用いて可動率を算出します。
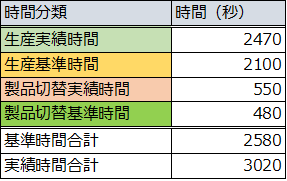
2580秒 ÷ 3020秒 = 85.43%となり、可動率は約85%となります。
今回、可動率についてご紹介してまいりました。生産性の改善指標として、よく活用される指標となります。
是非、ご活用をご検討頂ければ幸いです。
IoTの導入に興味のある方はこちらへ
生産性だけではなく、IoTを利用することによって、さまざまな現場の問題を改善することができます。とくに在庫110番では、IoTによる在庫管理を専門的に扱っています。
IoTの活用に興味のある方、導入してみたいけど、実際に「何から手を着ければ良いのかわからない」というときは、まずは在庫管理110番へお問い合わせください。