在庫管理アドバイザーの岡本です。
昨今、アメリカ西海岸の物流混乱や、東南アジアのコロナによる工場停止、ウクライナ・ロシア紛争等
によって、経験したことないような様々な問題が多発しています。
在庫管理110番のお客様からも下記のようなご相談が届きました。
昨今のウクライナ情勢により、仕入先からの納期(リードタイム)が長引いております。安定在庫数およびバッファー在庫設定にあたりこの影響をどのように反映させるべきか悩んでおります。リードタイムが不確定な場合はバッファー在庫を増やすという対策でよろしいでしょうか。欠品リスクを優先させた場合です。どの程度まで増やすべきか。教えてください。
恐らく、あなたも同じようなお悩みをお持ちではないでしょうか?
こんな時の対応方法について解説します。
目次
未来は誰にも分らない
前提としてあるのは、状況が完全に解消して元通りになるのが、いつであるか?は誰にも分らないという事です。
もし、わかる人がいれば、株を底値で買って大儲けしたりしているはずです。
また、このような時は、需要予測も役立ちません。
需要予測は、過去のデータを作ってモデル(数式)を作って、将来を予測します。つまり、過去に経験の無い事は予測できません。
非常時でも見通しさえ立てることができれば、先手が打てるので不安を減らせます。
しかし、見通しが立てられないと、何もわからないため不安しかありません。
誰にも分らない状況が発生した時こそ、見通し(見える化)が力を発揮します。
非常時における安全在庫の設定方法
非常事態の安全在庫の設定方法は、全く平時と同じです。
安全在庫は、バッファー在庫ですので「標準+α」のαが安全在庫に該当します。
現時点で標準を設定できているかどうかが、1つ目の重要なポイントになります。
例えば、部品や商品の仕入れであれば、標準調達リードタイムが設定されていること、生産であれば標準生産リードタイムです。
標準無ければ、バッファー無し。
標準が無い会社には「安全在庫」という言葉は、あってないようなものです。
まず、標準を設定します。
サプライチェーン全体を(仕入・生産・物流)で俯瞰する
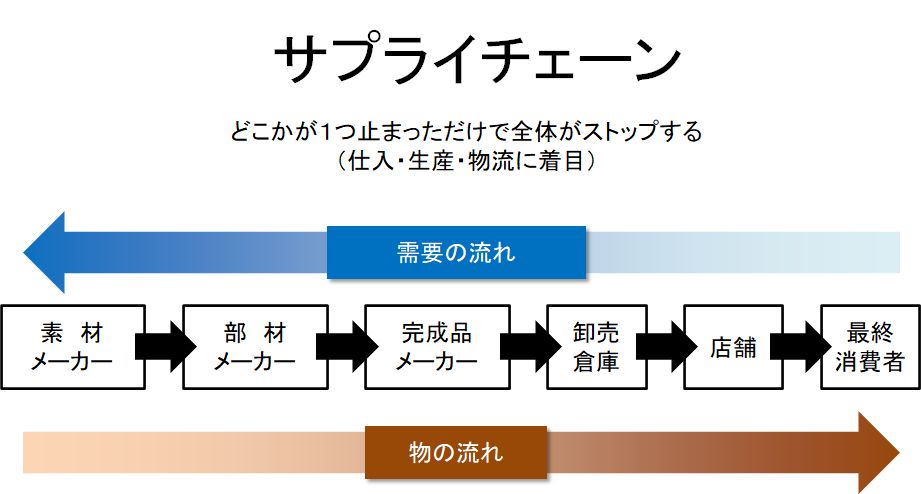
自社や仕入先だけではなく、関連するところまでサプライチェーン全体を俯瞰します。
あなたの会社が工場でなくても、仕入れる商品は必ず誰かが作っています。そして、その商品を作るための原材料が
必ずあります。例えば、衣類を考えてみましょう。
あなたが街で見る服が出来上がるまでを原材料から考えてみると、
- 原材料(綿花、羊毛など)
- 糸
- 染色
- 反物
- 裁断・縫製
といったような工程(セクション)を経ています。
なお、工場と工場の間には、中間業者となる倉庫業や卸売業(商社や問屋)が入るケースが多いです。
外部要因と内部要因
非常事態の安全在庫の設定に関わらず、安全在庫を設定する際は、外部要因と内部要因に分けて考えます。
- 外部要因:自社の努力では改善・解消できないこと
- 内部要因:自社の努力で改善・解消できること
例えば、今回のウクライナ・ロシア紛争の場合、「終戦」は自社でどうすることもできず外部要因です。
ウクライナやロシアから輸入している原材料や部品等は一見、外部要因のように見えますが、違います。
代替調達や設計変更による使用材料の変更を検討できるので、一部は内部要因です。
管理や改善の習慣ができていない会社は、普段から何かあったときは、全て外部要因化する傾向があります。
外部要因化すると、「自分では対処しなくても良いこと」になるので、その時点で対応が止まってしまいます。
逆に、管理や改善の習慣のある会社は、「自分たちでできることは何かないか?」ということを考えます。
この差はとても大きいです。
例えば、半導体不足問題で、自動車メーカー各社は大きな打撃を受けました。
大部分の会社は、「自社の事ではないから仕方がない」で終わってしまっているのではないでしょうか?
しかし、この事態をテスラは最小限に抑えました。
テスラは、対象の半導体を使わないで済むソフトウェアの変更だったり、半導体の内製化です。
参考記事
テスラだけではなく、日本国内のトヨタ自動車も素早い対応を見せました。
もちろん、影響が全くないわけではないと思いますが、何もしておらず、急に慌てている会社よりは
先手で経営的な判断(資金調達等)が打てるので、想定内で影響を受け止められます。
このようなことは一朝一夕でできることではありません。普段(平時)の管理がモノを言います。
サプライチェーンの中で起こりうるリスクを想定し、確認する
現状のサプライチェーンを把握した後は、サプライチェーンの中で起こりうることを想定します。
それぞれのセクションにおいて、仕入れ・生産・物流で精査します。
例えば、部品の調達が遅れている場合で想定されるのは、仕入先の
- 仕入:生産に必要な原材料や部品の仕入が遅れている(うまくいっていないのでは?)のでは?
- 生産:生産が間に合っていない。具体的には、生産能力を超えている、生産能力が足りなくなっている(設備故障や人員不足)等
- 物流:輸送手段の遅延。具体的には、工事などによる交通渋滞、繁忙期等によって輸送確保できていない、輸送能力を超えている、物流人員不足等
上記のうち、何が影響を与えているのかを見つけます。
この時、自社だけの力ではもはや無理な事の方が多いです。仕入先や物流業者の協力を得て、情報収集をします。
情報収集を依頼する際には、「とにかく何が影響を与えているかを調べてくれ」と曖昧な指示をせずに「仕入れ・生産・物流に着目して調べてほしい」
といったように具体的に依頼します。
起こりうるリスクの確度と頻度を知る
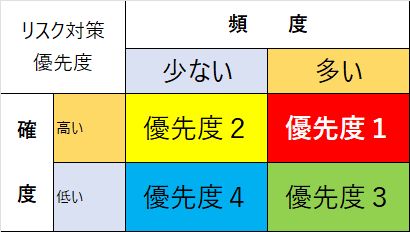
「起こりうるリスクを調べてほしい」と依頼するときに、気を付けてほしいことがあります。それは「確度」です。
- 確度とは、情報の確からしさ(どれくらい正しいか)ということです。
- 頻度とは、起こる回数のことです。
情報提供先は「確度」が低い情報を、出してこない可能性もありますが、この時は確度の低い情報も遠慮なく出してもらうようにします。
情報提供を依頼するときは、「確度の低い情報も遠慮なく、リスクがどれくらいの頻度で起こっているかもわかればお願いします」と伝えましょう。
確度も大切な判断材料の1つです。
確度が高く、頻度の大きなリスクが最も対策優先度が高いリスクになります。
ケースを3パターン程度用意する
様々なところから情報を集めると、
- どのようなリスクがあるかが分かる
- リスクの確度と頻度が分かる
これらの情報をもとに、安全在庫とモニタリング期間を設定して計画(想定)を立てます。
- 安全在庫はリスクをどれくらいカバーするか?
- モニタリング期間は、計画をいつ振り返るか?(安全在庫の見直し)
です。
計画(想定)を立てたうえで、少なくとも次の3パターンを作ります。
- 計画通り
- 計画よりもリスクが小さかった(過剰在庫になる危険性がある)
- 計画よりもリスクが大きかった(欠品になる可能性がある9
リスクの大小については、計画との差異率(計画よりも○○%良い、○○%悪い)と
いったように数値化しましょう。数値化しないと、担当者によって良い・悪いの判断がばらつくため、意味がありません。
キーになる情報をモニタリングする
恐らく、様々なリスク要因があるため、モニタリングが大変になりそう・・・
と思うはずです。そこで、余裕のない場合は、これまで得たリスク情報の中で最も影響を与えている情報・根本情報をキー情報にします。
キー情報の多くは定性的な情報(例えば、紛争が終わった等)の場合が多いですが、定量的な情報に置き換えられるとより良いです。
(理由:定量的な情報は、良化・悪化を数値で追うことができるため、判断材料にしやすい)
キー情報は、3つ程度に絞りこみます。
非常時を乗り切ったフィリピンでのケース
私が実際に遭遇して乗り切ったケース「輸入品の遅延」をご紹介します。
起こったことは交通規制によって、物流が混乱して船便の大幅遅延が発生したことです。
マニラ市のトラック走行規制が解除−期待されるマニラ港の貨物滞留問題(JETRO)
発生したことを時系列に並べると下記のような状況です。
- エストラーダ市長が排ガス規制対策で昼間、トラックの通行を禁止
- トラックが夜しか走れなくなる
- その結果、港での荷物の受け取りができない、荷物を船に積めないことが発生
- 荷物下ろしを待つ船、積み荷を待つ船が港で滞留。
- 船が予定通りに発着できず、出荷が遅れる。
この影響によって、徐々に船が遅れ始め、最大で4週間船の遅延が発生しました。
この時、安全在庫を何日分どれくらい持つか?という事が課題でした。(この会社は、標準状態の設定はできていました)
この時、遅れを発生させた最も重要なファクターは、「エストラーダ市長による交通規制」です。
この解消が無い限り、遅延は解消しません。
しかし、その間にも解消に向けた対策の動きはありました。
- 船社は、船の速力を上げる
- 船社は、船の本数を増やす
- マニラ港だけではなくほかの港も開ける
この時、最初は、「ETA:入港予定日(船が港に入る予定日)」をモニタリング対象としていましたが、予定日と実際の日付の狂いが大きく、
確度が悪いため使い物になりませんでした。
そこで、船のオペレーションをしていた業者との打ち合わせを持ち、引き出した情報が「着岸予定日」でした。
着岸予定日とは、船が岸壁(ヤード)に実際に着岸する日付のことです。こちらを代替としました。
通常、入港日と着岸日にはほぼ日数差はありません。
しかし、ここで日数に開きが出る理由は、入港した船が海の上で着岸を待っている状態(通称:沖待ち)です。
これが、船の混雑の指標になります。
そこで、第2の情報としてモニタリングしたのは、沖待ちしている船の本数です。沖待ち本数が減れば、混雑が解消されている
という事が分かります。
交通規制の解除が一番の近道ですが、解除の見通しが立たないため、
- 沖待ち本数が減る
- 入港予定日と着岸日の差が縮まっている(日数差)
をモニタリング情報として設定して、モニタリング期間は1週間に設定しました。
モニタリング期間を1週間に設定した理由は、当時使用していた船は1週間に1回の発着だったことによります。
沖待ち本数と日数差には関係性があったので、沖待ち本数で遅れの日数を推定し、安全在庫を何日分持つかを決めました。
会社にある対象の部品類は、現在庫数と在庫回転日数をモニタリングし、過不足が生じていないかどうかをコントロールしていました。
システムを準備する
モニタリングと予実管理を手作業でやり続けるのは、他の業務もあり限界があります。
ただ、放置してしまうと、対策が後手に回りさらに忙しくなります。
そこで、モニタリングしたい情報の予実管理をシステム化します。
具体的には、
- 業者へのメールは自動設定(毎週、同じ曜日に送られる)
- 入手した情報の入力はパートさん
- 計画と実績の集計はマクロ
- 現在の在庫状況(現在庫数、回転日数)
といったかたちです。
「できない、やらない」は全て手作業でやろうとしているからです。時間が無いのはみんな同じ。
システム(仕組み)を作って、省力化・自動化します。
標準・現状把握・予実管理が大切
非常時に困らないためには、平時の管理にどれだけ基本に忠実な管理ができているかがとても大切です。
外部環境の影響は平等に影響を受けます。ただし平時から、
- 現状把握できている(サプライチェーン全体)
- 標準を設定している
- 予実管理を行っている
会社は、どういった影響が起こりうるかを冷静にかつ客観的に読めるので、先手を打てます。
また、システムも構築されているので、慌てることはありません。
普段から行き当たりばったりの管理をしている会社は、平時であっても状況を見通せないわけですから、急に今から慌ててもすぐに状況は良くなりません。
標準状態を決め、現状把握をして、想定されるリスクを洗い出して、モニタリングと見直しを繰り返す・・・
大企業じゃなくても中小企業でも取り組めます。
在庫管理の仕組み作りのご相談
非常時・有事になったときに焦らない在庫管理の仕組みをつくりませんか?
全体が混乱している時こそ、競合から一歩先に出るチャンスです。
在庫管理110番では随時、在庫管理に関するご相談を受け付け中です。(※無料個別相談は、1か月7社様限定なのでお早めに!)
【無料】在庫管理個別相談受付中