在庫管理アドバイザーの岡本です。 人為的なミスを一挙に解決する一番効果的な手段は、「バーコードなどの自動認識技術の活用」です。 近年では在庫管理システムにバーコードを導入する企業も増えてきています。 しかし、初めて在庫管理システムや自動認識技術を利用する場合、注意しておきたいポイントがあります。
そこで今回は、在庫管理システムに利用されるバーコードや自動認識技術について、在庫管理の専門家の立場から導入~活用方法を実践的に解説します。
目次
- 1 代表的な自動認識技術
- 2 バーコード(一次元シンボル)
- 3 QRコード(マトリックスシンボル)
- 4 RFID
- 5 画像認識
- 6 自動認識技術を導入するメリット
- 7 バーコードとPOS
- 8 在庫管理システムとPOS
- 9 POSで情物一致
- 10 バーコードを利用するための2つの最低限の条件
- 11 バーコードを利用するための2つの準備
- 12 小売業のバーコードの扱い方
- 13 製造業のバーコードの扱い方
- 14 バーコードスキャナについて
- 15 バーコードスキャナとしてスマホ・タブレットを利用する
- 16 各種バーコードスキャナの特徴
- 17 バーコードスキャナを使い分ける
- 18 棚卸で情物の不一致を発見する
- 19 ITシステムを使った棚卸作業のメリット
- 20 棚卸差異の原因を追究できる
- 21 棚卸は効率化すべき作業
- 22 循環棚卸とは
- 23 循環棚卸のメリット
- 24 循環棚卸の方法
- 25 カウントの頻度と時間をどうやって減らすか?
- 26 在庫管理システムとロケーション管理
- 27 ロケーション管理の重要性
- 28 ロケーション管理を実現するための準備
- 29 ロケーション管理の階層
- 30 どこまで細かい管理を求めるか
- 31 ロケーション管理には2種類ある
- 32 ITシステムを利用した柔軟なロケーション管理
- 33 ロケーション管理を入出庫・棚卸に生かす
- 34 ロケーション管理のメリット
- 35 ロット管理とは?
- 36 ロット管理の重要性
- 37 ロット管理は負担が大きい
- 38 ロット管理とバーコード
- 39 ロット管理とロケーション管理
- 40 ロット管理と在庫管理システム
- 41 在庫管理システムを導入するには
- 42 在庫管理システムに関するお問合せ
代表的な自動認識技術
まず代表的な自動認識技術について紹介しておきます。
以下の4つがあります。
それぞれの特徴やメリット・デメリットを見ていきましょう。
対象品の特性や導入コストを勘案して採用することをお勧めします。
バーコード(一次元シンボル)
光学的反射率の高い棒状のスペース部分と低い棒状のバー部分との組合せで情報を表示し,機械読取りを可能としたものです。バーコードは、一次元シンボルとも呼ばれています。 現在、最もポピュラーな自動認識技術で技術で導入コストも他に比べると最も安く済みます。
- スーパーやコンビニの商品
なお、バーコードにはいくつもの規格(JAN、CODE39・・・)があります。 それぞれのバーコード規格が特性をもちそれを活かすことが大切です。
1つのバーコードが持てる情報量は、英数字で30桁くらいまでとなっています。
QRコード(マトリックスシンボル)
X軸及びY軸の両方向に情報を表示し,機械読取りを可能としたものでマトリックスシンボルとも呼ばれています。
- スマホでの会員認証やURLによる表示
導入コストは、バーコードとほぼ同じです。 バーコードを読み取る場合は、方向が限定されていましたが、QRコードは読み取りが全方向から可能なので、使いやすさも飛躍的にアップしました。
QRコードの面積次第ではありますが、1つのシンボルに英数字2,000桁(バーコードの約67倍)くらいまでの情報を保持できます。 ※QRコードは株式会社デンソーウェーブの登録商標です
RFID
カード状またはタグ状の媒体に、電波を用いてデータを記録または読出しを行い、アンテナを介して通信を行う認識方法です。 少し理解がしずらいと思いますが、バーコードやQRコードは、リーダーなどを使って1点ずつ読みこみ作業が必要ですが、RFIDは、電波を用いているため、書き込みと複数タグ一括読み取りができます。
従って、電波の届く範囲内であれば、タグ自体が遠くにあっても書き取りと読み取りができます。 これが、バーコードとQRコードとの大きな違いです。 ただし、専用のハンディーターミナルが必要なので導入コストは高くなります。 RFIDは一つのタグに英数字30,000桁(QRコードの15倍)くらいの情報が保持できます。
- 電車の乗車に使われているICカード(広義でRFIDの一つ)
画像認識
カメラ等で、読込んだ画像データをコンピュータにより処理して、画像認識技術でモノを認識します。
- 鉄板やアパレルの反物
様々な形状になる端材管理を行う場合は、検討の余地があるでしょう。
バーコードやRFIDが使えない場合などに有効です。
自動認識技術を導入するメリット
バーコードに代表される自動認識技術を、在庫管理システムに活用するメリットは3つあります。
- 人為的なミスが減る
- 作業の効率化
- 作業の標準化
リアル化による情報が同期化されたネットワークインフラとの相乗効果で人為的ミスの防止はもちろん、作業の効率化や標準化のメリットが享受できます。
かつてはハンディーターミナルが高価でした。またネットワークの構築を行うためには高額な投資が必要だったこともあり、大企業など一部の企業に導入が限られていました。
しかし近年、飛躍的に低価格化がすすんでいます。 バーコードやQRコードに至っては専用のハンディーターミナルが不要で、みなさんがお持ちのスマートフォンやタブレットなどのモバイル端末で代用できます。
バーコードとPOS
バーコード活用の典型的でわかりやすい例として、コンビニに設置してあるPOSがあります。
POSとは、「販売時点情報管理(Point of sale system)」の略のことで、物品単位で販売するたびに情報を記録するシステムです。
【POSの活用イメージ】
例えば、ある顧客がコンビニでパンを1個買います。
そのパンには「4903110079118」というJAN規格の商品コードがバーコードに変換され、印刷されています。
【POSを活用する最大の利点】
商品のバーコードをPOSのバーコードスキャナで読み取るだけで、リアルタイムでサーバーから商品名や価格情報が取得できます。
さらに、機能を拡張すればレシート印刷と支払精算ができます。
在庫管理システムとPOS
POSを在庫管理システムと連動させることも可能です。
パンが1個売れた場合で、見てみましょう。
バーコードスキャナの読み取りと同時に、顧客には関係ないところで店舗在庫からそのパンが1個出庫処理され、かつ在庫が1個減ります。
つまり、現品の動きとデータの動きの一連の作業がとても効率よく行われるということです。
間違いが発生することがほとんどありません。
POSで情物一致
在庫管理の大きな課題として、「情物一致」があります。
POSをうまく利用することで、この問題を解決できます。
例えば、作業内容や手順を誤った場合。
- ブザー音で通知
- 画面表示で警告
といったことが可能です。 人為的ミスを防止することができるわけです。
これを在庫管理システムの「出庫作業」に置き替えてみましょう。
作業者が持つモバイル端末がPOSになり、出庫品のバーコードを読むだけで出庫処理と在庫更新が同時になされます。
もちろん、出庫の指示が端末上に表示されていれば、商品違いや数量入力ミスは即座に端末が教えてくれます。
人為的ミスの防止と作業の効率化を同時に実現することができます。
しかし便利な自動認識技術ですが導入にはいくつかの留意点があります。
バーコードを利用するための2つの最低限の条件
バーコードを利用するためには、必ず最低限の条件が2つあります。
- SKU(単品在庫管理単位)ごとに品目コードが設定されていること
- 品目コードがマスター登録されていること
これらが整っていないとバーコードは利用できません。 もし品目コードが無い場合は、まずコード設定が最優先になります。 品目コード以外にも、バーコードで情報を管理したい場合は、管理対象がコード化されており、それがマスターが既に存在すること必要です。 すなわち、以下のことが必要となります。
バーコードを利用したい=コードの設定+コンピュータへのマスター登録
まずは、このポイントをご理解ください。
バーコードを利用するための2つの準備
バーコードがコンピュータに登録されたら、次はそれを利用するための準備が必要です。 情報媒体としてのバーコードの存在は、大きく次の3パターンに分類できます。
- 現品に直接印刷されている
- バーコードが印刷されたラベルが現品に貼られている
- 現品の近くにバーコードが印刷された印刷物がある
上記3つのいずれかにバーコードが印刷または貼り付けてある必要があります。 そして、次にそれを読み取るための器械である「バーコードリーダー」が必要になります。
自動認識システム=印刷されたバーコード+バーコードリーダー
この2つが揃って初めてバーコードが「自動認識システム」として利用可能となります。
バーコードは、業界にとって扱い方が異なるため、小売業と製造業を事例に説明しておきます。
小売業のバーコードの扱い方
スーパーやコンビニなどの小売業を見てください。
商品には必ずバーコードがついています。
世界共通の13桁のJANコードと言われる「バーコード」が付いており、それをそのまま商品コードとしても利用しています。 仮にバーコードが付いていないモノが入荷されても、その商品コードのバーコードを作り、ラベルを印刷して貼付すればよいことになります。
製造業のバーコードの扱い方
小売業と製造業ではバーコードの扱いが大きく違います。
製造業の場合、仕入れる原材料や部品には殆ど「バーコード」は付いていません。
仮に、付いている場合でも原材料や部品のメーカーの社内用コードであり、小売業のような世界共通のコードではありません。
したがって、仕入れた原材料や部品のコードをそのまま利用できないという問題があります。
この解決策として、仕入れた時点でバーコードラベルを印刷して貼付することになります。
バーコードを作る頻度と在庫の形態
また、製造業の場合は、小売業と違い仕入れた材料が加工されます。
そして在庫の形態は、「材料」→「仕掛品」→「製品」と次々に変化します。
仮に上記の方法を採用すると、在庫として存在する全ての品目(製造工程の仕掛品や中間品、最終製品など)を管理する場合は、その都度1品・1回ごとにバーコードラベルを印刷し貼付けしなければなりません。
この方法は、バーコードラベル発行や貼付の手間、ラベル消耗品代やラベル印刷機の導入に費用がかかり、コストがかかりすぎます。
省力化や作業品質向上のためのバーコードを導入したはずが返って、会社の生産性を落とす危険性もあります。
バーコードを使うにも工夫が必要
バーコードを導入するからには生産性を向上させないと意味がありません。 そこでバーコードの扱いにも工夫が必要になります。 工夫すべきポイントは、次の3点です。
- バーコードラベルの発行
- バーコードラベルの貼付け
- バーコード自体のコストダウン
仕入れ時に現品についているバーコードをそのまま利用
まずは現品に付いてくる仕入先の品目バーコードを、「そのまま利用する方法」があります。
コンビニなどの商品についたJANコードを、そのまま自社内の品目コードとして利用する例はその典型です。
同一品目が自社内品目コードと仕入先品目バーコードが異なる場合は、現品の仕入先品目バーコードを読むと同時に自社品目コードに変換して処理します。 この方法を採用する場合の注意点は、仕入先が品目コードを勝手に変更する恐れです。
対策としては、以下の通りです。
- バーコードの内容の変更に対して両社で取り決めを作っておく
- 仕入先がバーコードを変更したら連絡を受け、対比テーブルをメンテナンスするなどの対応をする
バーコードの印刷方法
前もってバーコードラベルの発行が可能な場合は、据置型の専用ラベル印刷機で印刷します。
しかし、専用機の価格はとても高価です。
そこで、プリンターで印刷するのが良いでしょう。
なお、プリンターでバーコードを表示する場合は、バーコード専用のフォントが必要です。(無料のものと有料のものがあります)
使い勝手を確かめるために無料から始めてみるのもいいでしょう。
バーコードの運用に慣れ、かつバーコードを発行する対象が増えてきたときに、必要性を感じれば、バーコードをプリンターで印刷する工数と時間と導入費用を比較し、費用対効果が見込まれる場合は専用機を導入することをお勧めします。
モバイル機器を利用した印刷
事前にバーコードラベルの発行し準備をしておきます。
そして、モバイル端末に接続された携帯ラベルプリンタから都度、印刷して貼付します。 最近のプリンターは安い機種でも、wifiなどの通信機能を備えています。
物流の激しい現場では特にこの方法が有効です。
現品以外にバーコードを貼り付ける
現品にラベルが貼りにくいモノの場合やラベル消耗品のコストを削減したい場合は、「入荷指示書」や出「荷指示書の品目コード」の横に品目バーコードを印刷しておきます。
入庫や出庫をするときに対象の現品の品目バーコードを読む方法があります。(バーコードの使いまわし)
さらに同一商品がまとまって保管される場合は、個別の商品にバーコードラベルを貼るのではなく、その商品の保管棚やパレットに代表の商品バーコードラベルを1枚だけ貼るなどで消耗品とそれを貼る手間が削減できます。
バーコードスキャナについて
バーコードを読み取るためにはバーコード・スキャナが必要です。 在庫管理の現場での実際の読み取り作業はモバイル端末で行います。
次の機器が挙げられます。
- バーコード・スキャナを内蔵した機器
- 端末に外付けのバーコード・スキャナを接続した機器
モバイル端末としては、専用機のハンディターミナルとそれに代わる機器としてスマートフォンやタブレットがあります。
バーコードスキャナとしてスマホ・タブレットを利用する
以前はバーコードスキャナと言えば、専用機しか選択手段がありませんでした。
しかし、スマートフォンやタブレットが普及して、バーコードスキャンの機器として代用できるようになりました。
ハンディーターミナルと比べると導入のコストが安いのが利点です。 一方で、読み取り機器としての課題が残っています。
スマホ・タブレットの問題点
スマートフォンやタブレットの代表的な搭載OSとしてはiOS、Android、Windowsがあります。
それぞれ開発言語が異なりアプリの互換性はありません。 専用機と違い、スマートフォンやタブレットの活用は「堅牢性」に弱点があります。 バーコードスキャナが使われる場所は、事務所ではなく倉庫などの現場です。
落下や衝撃を受ける危険性がとても高いです。 スマートフォンやタブレットは一般的にそんなに耐久性が強くなく、「現場」を考えた時に疑問符が付きます。
また、頻繁なOSのバージョンアップ対応や機器の寿命も2~3年と短く「同一機種の入手性」にも問題があります。
1年後にはもう同じ機種は生産されていないことが多いので、利用を拡大しようと思っていたらすでに機種の生産が終了していた、サポートが切れていたといった問題に直面する可能性もあります。
とはいえ、導入のしやすさは魅力的ですし、いきなり専用機を導入するのはハードルが高いため、利用シーンによりそれぞれの機器の特徴を活かして使い分けることをお勧めします。
各種バーコードスキャナの特徴
代表的なバーコードスキャナの特徴をご紹介します。 比較するポイントは次の3点です。
- ハードの費用
- バーコードの読取性能
- 機器の操作性
紹介の順番は、バーコードスキャナとしての性能が高いものから順に紹介しています。
- ハンディターミナル
- スマートフォンをジャケット型外部スキャナーで包む一体タイプ
- タブレットと外部スキャナーとをBluetooth通信でつなぐ分離タイプ
- スマートフォンと外部スキャナーとをBluetooth通信でつなぐ分離タイプ
- スマートフォンの内臓カメラをスキャナーの代用をさせるタイプ
1.ハンディターミナル
ハンディターミナルは、バーコード・スキャナ内臓タイプの専用モバイル端末です。
バーコードスキャン用の機器として昔から利用されています。
ハンディターミナルは専用端末なので、操作性・読み取り性能ともに良く、堅牢であるため在庫管理の現場端末としては一押しです。
各社から様々なハンディターミナルが販売されています。 大きな違いは採用しているOSと開発言語です。
各メーカー独自のOSや開発言語を持つものとマイクロソフトのWindows OSを搭載したメーカー共通のものとがあります。
メーカー独自OSの端末の場合、他のメーカーの端末に変える場合、アプリは作り直す必要があります。
一方でWindows OSの端末は、他のメーカーの端末に変えてもアプリはほぼそのまま使用できます。スマホにアプリをダウンロードできるので、とても手軽です。 難点として、端末の価格が高く、台数が多くなると導入コストがかさんでしまうことです。
2.スマートフォンをジャケット型外部スキャナーで包む一体タイプ
スマートフォンにジャケット型外部スキャナーの費用が加わります。
外部スキャナーがスマホと一体となり片手で操作できます。
読取速度も含めて、ハンディターミナルに近い操作感が得られます。
デメリットは、機種が変わると外部スキャナーが使えなくなる恐れがあることです。
3.タブレットと外部スキャナーとをBluetooth通信でつなぐ分離タイプ
タブレットに外部スキャナーの費用が加わります。 外部スキャナーは専用なのでハンディターミナルと同等の読み取り速度が得られます。
ジャケット型外部スキャナーの場合は、機種が変わると使えなくなる恐れがありました。
しかし外部スキャナーはその心配が無く、タブレットが変わっても利用できます。
タブレットはスマートフォンに比べて表示画面が大きいため、入出庫指示を伴う検品業務や棚卸業務では紙を無くすことにも役立ちます。
小売の場合はモバイルPOS端末として利用できます。 (イベント会場などで利用されるケースが増えてきました)
難点としてはタブレットと外部スキャナーを持たなければいけないので、片手で操作できません。
両手が塞がってしまうので操作性に問題があります。
また読み取り速度がジャケット型外部スキャナーに比べるとやや劣ります。
4.スマートフォンと外部スキャナーとをBluetooth通信でつなぐ分離タイプ
基本的には表示画面がタブレットに比べて小さいだけで機能、性能面ともスマートフォンと外部スキャナーをつなぐ③の場合と同等です。
取扱品目の少ない場合や多人数で一斉作業する棚卸業務などに有効です。 両手がふさがってしまうということと、画面が小さいので見づらいという難点があります。
5.スマートフォンの内臓カメラをスキャナーの代用をさせるタイプ
一番コストを掛けずにバーコードスキャンを導入する方法です。 必要なのはスマートフォンのみです。操作は写真撮影と同じようになります。
難点としては、写真撮影と同じなので、スマホでバーコードに焦点を当てるのに時間がかかります。
読み取り速度もハンディターミナルに比べて、かなり劣ります。
実際に現場で作業をすると分かりますが、バーコードの読み取りに時間がかかるととてもイライラしますし、生産性も落ちます。
バーコードスキャンを利用する回数が少ない場合、例えば取扱品目の少ない場合などに有効です。
バーコードスキャナを使い分ける
以上のご紹介したモバイル端末は、開発費を節約するためにシステムとして、「どれか一種類に統一して導入する」のが一般的です。
しかし、拠点数や利用時期の集中度によっては、同じアプリを複数種類の端末に対応しておくことも有効です、
例えば、地方の営業所にはスマートフォン、物流センターの棚卸にはハンディターミナルとタブレットというような導入方法によってトータルの端末コストを抑えることができます。
棚卸で情物の不一致を発見する
これまでご説明したITを活用し、モノの動きに同期化した在庫管理システムが稼働しているとしても、注意しておきたいポイントがあります。
それは人が介在する限り、100%ミスは防げないという点です。
その不一致を見つける手段として「棚卸」があります。 棚卸には次の目的があります。
棚卸の目的とは何か?
- 決算の経営数値を固めるために現品を数えて棚卸資産が実際に存在しているかを確認すること
- 現品数とシステム上の在庫数の差異を調査・分析して在庫管理システムがうまく機能しているかどうかその有効性を確かめることです。
- ひとつひとつ、現品を数えるため商品の品質チェックが可能になる。 棚卸をやりっぱなしではなく有効に活用する
一般に「棚卸」は1つ目の会計決算上の目的に主眼が置かれてきました。
年1回現品在庫が正確に把握できればそれで終わり、という「義務的な作業」としてとらえている企業が多々あります。
棚卸は在庫管理システムの監視機能を持っている
一方で、棚卸は在庫管理システム全体の観点から重要と言えます。すなわち、「システム監査機能」という大事な役目を持っています。
ITを活用すると、現品の動きに情報が同期化した在庫管理システムになります。
よって棚卸に付随する様々な作業やデータ処理をできるだけ省力化して実行できる「棚卸サブシステム」が実現できます。
ITシステムを使った棚卸作業のメリット
「棚卸サブシステム」は以下のような手作業で行う棚卸では実現できない機能を持っています。
- 棚卸の結果(品目コードや数量、場所などの棚卸し情報)をいちいち手書して、さらにパソコンに入力する必要がなく、商品のバーコードスキャンし、実棚数を入力するだけで効率よく入力できる
- 棚卸の入力と同時に棚卸結果がリアルに集計できるので、コンピュータ上の帳簿在庫数と比較した差異が即座に確認できる
- 保管場所の確認については、ある商品の棚卸数量を入力する時にその保管場所のバーコードもスキャン入力することで、所定場所単位ごとの差異把握や同一製品の複数保管場所把握などが可能である
- 棚卸時に気付いた現品の品質情報が入力できる。例えばコメント欄を設け、「錆びあり」、「積み方危険」などの情報を選択または自由入力ができ、個々の商品の品質管理に役立つリアルな情報が得られる。
棚卸差異の原因を追究できる
特に在庫管理にITシステムを導入した時に力を発揮するのが、棚卸差異の原因を追究する場面です。 例えば、次のようなメリットが考えられます。
- 日常の入出庫情報にはデータ種や入力者名、入力日時などの追求しやすい情報を自動的に付加するようにしておくと、過去の入出庫情報をあらゆる角度から簡単に検索できる。その結果、棚卸差異の原因を効率よく調査することが可能になる。
- 差異の原因をいくつかコード化しておくことで、差異発生の原因がわかった時に、在庫修正データの入力する時に原因コードも入力することができます。その集計結果がシステムの改善ポイントに結びつけられます。 例えば、出庫の入力漏れがあり、その原因がサンプル出荷の入力漏れであり、同じ原因による差異が3件あったとするとサンプル出荷の出庫処理の手順に問題があるということが浮き彫りになります。 棚卸差異の分析の結果から、「出庫の手順」の改善が必要ということが判明します。
棚卸は効率化すべき作業
これまで説明をしてきたいわゆる「一斉棚卸」は、1日から数日間も一切の入出庫を停止して社員総動員で行う作業です。もともと棚卸自体は利益を生みません。 バーコード活用などで棚卸作業が効率アップ出来たとしても、「一斉棚卸」はコスト面や精神面で問題があります。
したがって、より効率的な仕組みが求められます。 そこで、ITの力を最大限に活かして「棚卸」をより効率よく行える手法として「循環棚卸」(サイクルカウント)があります。
循環棚卸とは
一斉棚卸が「全品目を棚卸する」のに対して、循環棚卸は「年間スケジュールを作成しておき、そのスケジュールに計画された品目のみ、カウントする方式」です。
つまり全品目ではなく、一部の品目に対してのみ棚卸を行う方法」です。
循環棚卸のメリット
循環棚卸には以下のメリットがあります。
- カウント時に適宜、数量差異や保管場所差異を見つけることができる。そのため、原因追及と改善が一斉棚卸に比べて簡単になり、在庫管理システムの監査機能が強化できます。
- 入出庫停止時間帯を分散し負荷の最小化ができるので生産や販売のロスが防げます。
- 工夫をすればほぼ生産や販売活動を全く止めずに棚卸ができる。
- カウントする人を専任化できるため、カウントミスが起こりにくくなる。さらにエラーの原因追及が早くなります。
- 保管場所の即時修正ができる。帳簿上の在庫品目のロケーションに違いがある場合はその場で是正することができます。
循環棚卸の方法
では循環棚卸はどうやって行えば良いのでしょうか。 カウント対象を決める方法としては、ゾーン方式とABC区分方式があります。
ゾーン方式
これは保管場所を基準にしてカウント対象を決める方法です。 具体的には、保管場所の区画を指定して区画別のカウントスケジュールを設定する方式です。 品目を決められたところに保管する固定ロケーションを採用している場合や仕掛品、積送品などの荷動きの速い品目に有効です。 この方式が日本では循環棚卸の代名詞のようになっていますが、単純に一斉棚卸を分割・分散しただけのスケジューリングをしているケースが多く、あまり合理的な方法とは言えません。
ABC区分方式
ABC区分によって棚卸の対象を決める方法です。 具体的には、使用金額ベースや入出庫頻度ベースでABC分析で 決められたABC区分別にカウント頻度を決める方式です。 例えば、Aアイテムは月1回、Bアイテムは3か月に1回、Cアイテム は12か月に1回(年1回)としてカウントスケジューリングをします。 これにより、合理的かつ品目の重要度によって管理に重みづけをすること ができます。
【関連記事】
カウントの頻度と時間をどうやって減らすか?
次にカウント時期については一定間隔で指定することもできますが、カウント工数を削減するスケジューリングを、在庫管理システムに組み込むことができます。
例えば以下のようなタイミングです。
- 注文を出すとき・・・在庫水準が少なく、かつ注文エラーを防止できる
- 注文受入直前・・・在庫水準が最も少ない
- 在庫がゼロになったとき・・・・帳簿在庫がゼロになった時に行う
- 入出庫件数が一定数を超えたとき・・・差異の発生度合いが多いはず
- 異常値が発生したとき・・・帳簿在庫がマイナス数値になったときや現品行方不明の時
以上から、
- 「棚卸」が在庫管理システムの情物一致の監査機能として大事な役割をもっていること
- 「循環棚卸」その役割に最も適していること
がお分かりいただけたと思います。
これもITを活用し、モノの動きに同期化した在庫管理システムが稼働しているからこそできる仕組みです。 狭義の情物一致は、品目ごとの数量のデータと現物が合っていることを指しますが、実際に求められる情物一致は、
- ロケーション(置き場)
- ロット
- 賞味期限
などの在庫の物流や品質に関する情報が一致していることも含みます。 これらの情報は通常では管理・監視が難しいですが、在庫管理システムなら、かんたんに管理し、状況を監視することができます。
在庫管理システムとロケーション管理
在庫管理システムの基本目的である「何が、いくつ、どこにあるか」のうち、「どこにあるか」を明確にするためのロケーション管理は情物一致の重要な機能です。
また、現品管理の核となる5Sのうちの整頓のキモとなる3定の実現にも不可欠な要素でもあります。 ➽在庫管理の基本と重要性はこちらでご確認ください
ロケーション管理の重要性
ロケーション管理とは「在庫の置き場」を管理することです。 在庫管理の現場では、在庫の置き場が分からない、あるはずの在庫が見つからないということが非常によく起こります。
例えば、倉庫を3つ持っている会社に品目Aが100個あったとします。 3つの在庫数は以下の通りです。
- 倉庫Aに20個
- 倉庫Bに80個
- 倉庫Cには0個
ロケーション管理をしていれば、倉庫Aもしくは、倉庫Bにそれぞれ、いくつ在庫があることが分かります。
しかし、ロケーション管理をしていなければ、倉庫Cにあると思っていた担当者が「在庫が無い!」と困ることになります。
担当者は、倉庫Cの中を探し回るかもしれません。 在庫が狂っていると思いこむかもしれません。
このように勘違いや非効率な作業を予防するためにもロケーション管理は、在庫管理においてとても重要です。
ロケーション管理を実現するための準備
まず、ロケーション管理を行うための準備が必要です。 品目コードと同じように、保管場所を示すロケーション番号(番地)を決めなければいけません。
ロケーション番号の附番の方法は、「作業効率の面からピッキングの導線に沿って行う」のが基本原則です。
また、ロケーション番号の粒度(例えば、何ゾーンの何番の棚の何段目の何間口などの階層の深さ)は、入出庫担当者が専任の社員中心かアルバイト中心かなど担当者の熟練度によって変わります。
ロケーション管理の階層
ロケーション管理には階層があります。 大きく分けて下記です。
- 会社レベル・・・会社全体の在庫
- 支店レベル・・・各拠点(工場や営業所など)にある在庫が分かる
- 倉庫レベル・・・拠点内にある保管場所(建屋単位)で在庫が分かる
- ゾーンレベル・・・倉庫の中の区画(エリアやブロック)
- 列レベル・・・棚が並んだひとつのラインレベル
- 連レベル・・・列の中のひとつひとつの棚
- 段レベル・・・置き場の高さ方向の在庫が分かる
- 間口レベル・・・段の中の商品別の仕切り
中小企業の多くは良くて「会社レベル」の在庫管理止まり、つまり会社内に在庫がいくつあるかが分かっているにすぎません。
例えば、支店レベルまでロケーション管理ができている会社では、A支社に〇〇個、B支社に××個と言った具合に、各拠点谷の在庫が分かります。
どこまで細かい管理を求めるか
あまり細かな粒度のロケーション番号の附番は、現場のロケーション管理の手間を増すので逆効果を生む場合があります。
ある中小企業に在庫管理システムの導入時に、規模があまり大きくない倉庫で正社員が入出庫作業を行う利用環境にも関わらず、詳細なロケーション番号の附番を強いたことがあります。
その結果、現場の作業負担が増えてしまったため、ゾーン程度の粗いものに設定し直したという苦い経験があります。
管理者としては細かくすればするほど、品目単位ごとのロケーションが明確になります。
一方で、上記のような現場の作業負担になったり、ロケーション管理システムのメンテナンスに工数がかかってしまったりします。
【point!】
企業規模や人員構成、取扱製品などの会社の状態を考慮してロケーション管理の粒度を決めていく必要があります。
ロケーションの附番が終わったら、ロケーション番号をバーコード化し、ラベル印刷して所定の場所に貼付します。 (バーコード管理を導入している場合に限る)
ロケーション管理には2種類ある
実際に商品とロケーションを紐づける保管ルールには 大きく分けて次の2つがあります。
- 固定ロケーション
- フリーロケーション
固定ロケーション
「固定ロケーション」は、アイテム毎に保管する場所を決めて運用します。
例えば、出庫頻度によるABC分析を行い、出庫頻度の高いAアイテムは、取り出しやすい場所に「固定ロケーション」として割り当てるなどの重点管理が活かせます。
保管場所が固定化されるため、在庫の場所が常に確定できるので分かりやすいです。
しかし、在庫が無い場所に他の在庫を置くことはできません。
空きスペースが生まれやすく、スペース効率が悪いため、柔軟性に欠けることが弱点です。
フリーロケーション
「フリーロケーション」は、品目をロケーションに固定せず空いている場所に保管していきます。
フリーロケーションは手作業では難しいため実現するためには、システム化されたロケーション管理が必須です。 空きスペースを次々と埋めることができるため、スペース効率が良く、現場の運用はとても柔軟なのが特徴です。
特にフリーロケーションは、次のような動きの激しい在庫品目に向いています。
- 雑貨やアパレルのような需要変動や製品の流行や入れ替わりが頻繁にある商品
- 化学原料のような生産量の変動で在庫の増減が多いもの
- 食品・医療のような日付管理やロット管理が必要な商品な
ITシステムを利用した柔軟なロケーション管理
IT利用の同期化した在庫管理システムなら、「固定ロケーション管理」と「フリーロケーション管理」を併用した柔軟な運用も可能です。
例えば「同じアイテムは同じ所に置くのが原則だが、場所がなければ空いた所に置く」や「Aゾーンの商品は固定ロケーション、Bゾーンの商品はフリーロケーション」という運用ができます。
ロケーション管理を入出庫・棚卸に生かす
ロケーション管理の発展的な利用方法を紹介します。
「入庫指示書、出庫指示書、棚卸表などにロケーションを表示」→「入庫、出庫、棚卸などの作業の際にロケーション順に動いてロケーションと品目のバーコードを読み込む」という方法です。
自動的な入力が可能となり、誰でも効率的な作業ができるようになります。
ロケーション管理のメリット
ロケーション管理は単に「どこにある」を知るだけでなく、「作業の効率化」や「スペースの有効活用」に大きな貢献をします。
従って、棚卸が品目と数量の監査だけでなくロケーションの監査と調整を兼ねていることがご理解いただけたと思います。
ロット管理とは?
最近はトレーサビリティ、鮮度管理、品質管理に対する要求が厳しくなってきています。
これらの要求に対して在庫管理システムはどう対処したらよいでしょう。
「何が、いくつ、どこにあるか」の「何が」は、通常は品目のことを指します。 食品などの品目によっては、さらに賞味期限管理が必要です。
そのため、品目を作った製造日付単位での品目管理が要求されます。 その製造日付別の品目の集まりを一つの製造単位として「ロット」と言い、ロット別に品目を管理することを「ロット管理」と言います。
ロット管理の重要性
ロットはし、品目情報と親子の紐づけをします。 主にロット管理は、客先でのトラブルが発生した時の原因追跡を支援するトレーサビリティに威力を発揮します。
さらにロット情報を利用して鮮度管理や品質管理を行うことができます。 商品マスタに品目別の期間情報を登録しておくことで、製造日付から賞味期限や使用期限などの期限情報が算出できます。
それらの期限を利用して鮮度管理や品質管理を行うことが可能です。
ロット管理は負担が大きい
ロット管理は、同じ品目に異なる製造日付がつきます。 つまり同じ品目でも別々に管理をしなければいけないということになります。
例えば、同じ品目でもロットが3種類ある場合。
- 管理する品目-ロットのひも付ごとに管理しなければいけないため、管理対象が3倍に増える
- 同時に、入出庫や棚卸の情報量も3倍になる
- そのためロット管理は在庫管理担当者の入力負担がとても重くなる
しかも、物を動かす時には必ず賞味期限などの期限チェックや先入先出のチェックをしなければいけないため、処理自体も複雑になりがちです。
そのため、ロット管理は処理を人手だけに頼るのは人員的にも時間的にも無理があります。負担を軽減し、ミスを減らすためには在庫管理システム等の有効活用がより重要になります。
ロット管理とバーコード
バーコードには、ロット情報としてロット番号、製造日、製造番号(製造ライン)、製造担当者など多くの情報を含める必要があります。
そのため、1次元のバーコードでは容量が足りず、一般に二次元のバーコード(QRコード)が採用されます。
2次元のバーコード化のもとになるロット情報が得られるタイミングは、自社製造品の場合は製造完了入庫時、仕入商品の場合は納品入庫時に得られます。
その時点で2次元バーコ―ドラベルを作成・印刷し、現品に貼付し、ロット管理をすることになります。
ロット管理とロケーション管理
また、ロット管理を行うとロケーション管理にも工夫が必要です。 品目単位がロット情報を含むことにより、激しく変わります。
品目に対する固定ロケーション方式は不向きです。 ロケーション登録するフリーロケーション方式が必然になります。
ロット管理と在庫管理システム
以上のようにロット管理によるトレーサビリティ・鮮度管理・品質管理は、在庫管理システムの機能と密接に関係しています。
まさに物と情報を一致させるには、「2次元バーコード」や「ハンディターミナル」の活用と、リアルタイムな処理環境を備えた在庫管理システムの構築が規模の大小を問わず求められます。
在庫管理システムを導入するには
棚卸やロケーション管理、ロット管理は、いかに時間を効率化させるかがポイントです。 在庫管理システムを使えば、ムダな作業をする必要がなくなります。 と言っても、機能性が充実した高価な在庫管理システムを導入する必要はありません。 最低限の機能さえあれば十分です。重視すべきは、機能性よりも「現場での使いやすさ、操作性の良さ」。 弊社では在庫管理のプロが手がけた「成長する在庫管理システム」を提供しています。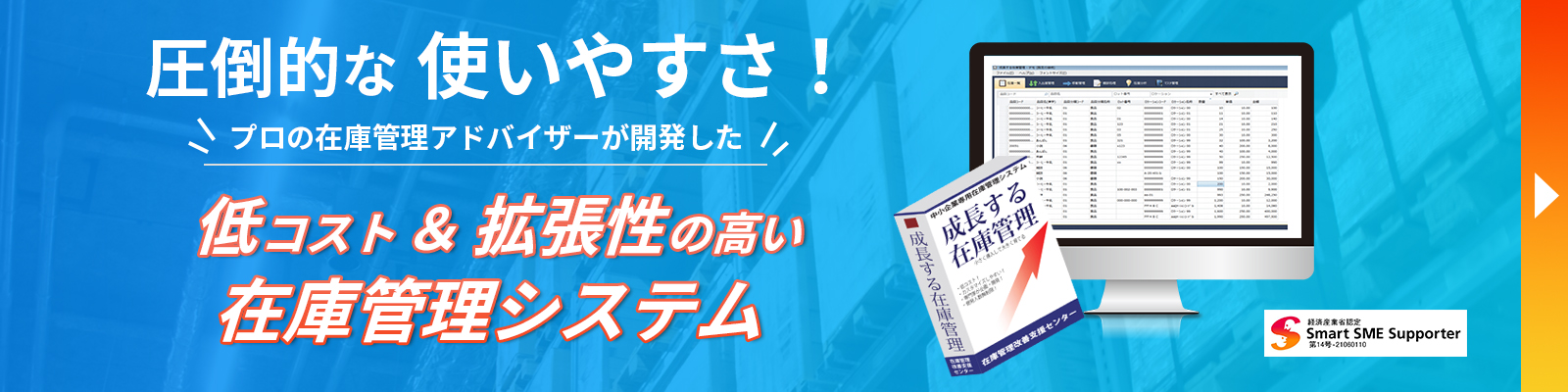
- ロケーション(移動元・移動先記録、メモ登録、検索機能(日付、品目コード、品目名、ロケーション、ロット)
- 棚卸(棚卸差異表示、棚卸結果の即時反映、全棚卸データ参照可能、一斉棚卸・循環棚卸に対応)
在庫管理システムに関するお問合せ
在庫管理110番では、在庫管理システムの新規導入、入れ替え、検討について ご相談を承っています。お気軽にご相談ください。