「自社の在庫、本当に『適正』ですか?」
もしかすると、「欠品でお客様を待たせてしまった…」「売れ残った在庫が倉庫を圧迫し、キャッシュフローが悪化している…」といった悩みを抱えていませんか?
企業の経営において在庫は「資産」であると同時に、「リスク」にもなり得ます。
在庫は多いのは分かっている在庫削減はしたいけど、減らしすぎは困る。。在庫をどれくらい減らせば良いのかが分からない・・・と、その「適正な量」を見極めるのは簡単ではありません。
この記事では、「適正在庫」とは何か基本から、その考え方や算出方法、維持するためのポイント、さらにより低減し安定させる方法まで実際にコンサルティングの現場で活躍している在庫管理アドバイザーがわかりやすく解説します。
- 安全在庫と適正在庫の違い
- 適正在庫の計算方法(経営的視点、実務的視点)
- 適正在庫を維持するためのポイント
- 需要予測を適正在庫の維持に取り入れる方法と注意点
- 【小売・卸売業向】適正在庫のさらなる低減・安定化を目指す方法
- 【製造業】適正在庫のさらなる低減・安定化を目指す方法
この記事を読めば、あなたの会社にとって「どれくらい在庫を持つのが最も効率的か」が見えてきます。ムダを減らし、必要な在庫だけを確保するためのヒントをぜひ見つけてください。
目次
- 1 安全在庫と適正在庫の違い
- 2 適正在庫を計算するために必要なデータの準備
- 3 適正在庫を計算する3つの方法
- 4 適正在庫を経営的観点から計算する方法
- 5 適正在庫を実務的観点から計算する方法
- 6 経済的発注量(EOQ)
- 7 適正在庫を見直して維持するための4つのポイント
- 8 需要予測を適正在庫の維持に取り入れる方法と注意点
- 9 適正在庫の実現・維持をサポートするためのシステム・ツール
- 10 適正在庫のさらなる低減・安定化を目指す方法(小売業・卸売業)
- 11 適正在庫のさらなる低減・安定化を目指す方法(小売業・卸売業)
- 12 まとめ
- 13 自社の適正在庫の計算方法が分かる在庫管理セミナー
- 14 適正在庫に関するご相談・お問い合わせ
- 15 適正在庫に関する関連記事
安全在庫と適正在庫の違い
まず、最初に安全在庫と適正在庫は違います。この2つはよおく混同されがちなので、最初にお伝えします。
適正在庫とは「欠品せず、かつ過剰在庫にならない適正な在庫数のこと」です。
適正在庫は、在庫数の上限値(過剰在庫)と安全在庫数に挟まれた幅の在庫数のことです。
安全在庫とは?
安全在庫は、適正在庫の構成要素のひとつと理解すると良いでしょう。
安全在庫は欠品を防ぐための在庫で在庫の下限値なので、過剰在庫は防げないため上限値も管理するのが適正在庫です。
在庫管理110番の相談者も、安全在庫=適正在庫と考えがちえですが、実は違います。
安全在庫の計算方法の具体的な解説はこちらの記事をご覧ください。
適正在庫を計算するために必要なデータの準備
適正在庫を計算するためには、以下のようなデータが必要になります。
- リードタイム: 発注から納品までにかかる日数(平均、最大、ばらつき)
- 需要実績: 過去の出荷量、販売量データ(※最低、3年分は必要)
- 発注ロット: 一回の発注量
- 欠品許容率: どの程度の欠品まで許容するか(安全係数の設定に必要)
これらのデータを日頃から正確に記録・管理しておくことが、精度の高い適正在庫計算の第一歩です。
適正在庫を計算する3つの方法
適正在庫の計算方法は、いくつかあります。主な計算方法を3つ解説します。
- 経営的観点:会社が理想とする決算目標から設定する
- 実務的観点:現場の実情に合わせて主にリードタイムを使って決めるボトムアップ方式
- 経済的発注量:発注するコストも考慮に入れて計算する方法
あなたの会社の取り組みやすい方法で、適正在庫を計算しましょう。
適正在庫を経営的観点から計算する方法
適正在庫は、会社が目標としている決算書(財務状態)で計算できます。
「会社が目指す在庫金額=適正在庫」という考え方です。
改善の土壌が整っていない会社は、経営的観点から適正在庫を決める「トップダウン方式」がお勧めです。
経営的観点から計算する方法は3つあります。
- 売上から計算する
- 在庫回転率から計算する
- 資金繰りから計算する
売上から適正在庫を計算する方法
目標在庫金額が決められない・・・という会社にお勧めの方法です。
売上に対する在庫金額の比率から計算する方法です。在庫金額の比率の計算式は、
在庫金額の比率=在庫金額÷売上
在庫金額が多すぎると、在庫金額の比率が上がります。
下の表は、業種別・売上規模別に、在庫金額の比率(赤枠部分)をまとめた表です。
各業種で、目安となる在庫金額の比率は、それぞれ次の通りです。
- 製造業:8%未満
- 卸売業:4%未満
- 小売業:4.5%未満
在庫金額の割合が15%を超えてくると在庫が多すぎると考えて良いでしょう。
利益率や同業種でも扱っているもので多少の誤差はありますが、売上に対して在庫金額の割合が15%を超えていると「在庫が多い」と認識して間違いないでしょう。
在庫回転率から適正在庫を計算する方法
在庫回転率とは、在庫の流動性(滞留度)を表す指標です。
- 在庫回転率が大きい:在庫の流動性が良いことを示し、在庫効率が高い。(商品が早く売れている、部品が早く使われている)
- 在庫回転率が小さい:在庫が滞留していることを示します。(仕入れた商品が売れるまでに時間がかかっている、仕入に対して売れ行きが少ない)
在庫回転率の計算式
- 在庫回転率=売上原価÷平均在庫(期首在庫と期末在庫の平均値)
- 在庫回転日数=期間(日数) ÷ 在庫回転率 ※日数とは期首から期末までの日数
会社が目指す財務目標から在庫回転率を計算します。
会社から目標が示されない、目標の設定の仕方が分からないという場合は、下記の表を参考にしてください。
ご覧いただくと分かるように、優良企業に比べて、赤字企業の方が比率の割合が大きいです。
目安となる在庫回転日数は、それぞれ次の通りです。
- 製造業:30~60日
- 卸売業:15~30日
- 小売業:15~20日
※カッコ内は在庫回転率
資金繰り(キャッシュフロー)から適正在庫を計算する
運転資金からも適正在庫を計算することもできます。
運転資金とは、会社を運営するために必要な現金(=いわゆる資金繰り)のことです。
この金額が少ないほうが、資金繰りが楽といえます。
キャッシュコンバージョンサイクル(CCC)とは?
資金繰りから適正在庫を計算する時に知っておきたい管理指標がキャッシュコンバージョンサイクル(CCC)で、投資した金額が何日後に返ってくるかを表す指標です。
例えば、例えば、CCCが90日の場合、今日100円で仕入を行った場合、その100円が戻ってくるのは約90日後ということになります。
つまり、この商品を毎日売り続けるためには、少なくとも9000円の借金が必要ということです。
CCCの計算式
CCC = 棚卸資産回転日数+売掛債権回転日数-買掛債務回転日数
計算項目の説明
- 棚卸資産回転日数:在庫回転日数のこと
- 売掛債権回転日数:いわゆる売掛。販売先への請求から現金が入金されるまでの日数
- 買掛債務回転日数:いわゆる買掛。仕入先からの請求を払うまでの日数
アマゾンは創業当初から赤字もしくはほぼ利益の無い状態にもかかわらず積極的な投資が行えたのは、CCCを経営指標として取り入れていたからだと言われています。
資本効率(手元にある資本を効率良く使って、どれだけの売上を上げたか?)を重視する現在欧米の企業では当たり前で、日本の上場企業も資本効率を意識しています。中小企業にとっても重要な経営指標になることは確実です。
キャッシュコンバージョンサイクルについて詳しく知りたい場合は、下記の記事をご覧ください。
適正在庫を実務的観点から計算する方法
次に実務的観点から適正在庫を計算する方法をご紹介します。
実務的観点から計算する方法は2つあります。
- 必要数から計算する方法
- リードタイムから計算する方法
適正在庫の実現・維持するより具体的な方法は以下のページで解説しています。
適正在庫の実現・維持のために実践できる10個の方法(全業種共通)
サイクル在庫から適正在庫を計算する方法
サイクル在庫とは、一定期間内の需要数(販売数や使用数)を満たすための平均在庫数(つまり必要な在庫数)のことです。
サイクル在庫から適正在庫を計算する方法
適正在庫=サイクル在庫+安全在庫
サイクル在庫数の計算方法
発注ロットからサイクル在庫を計算する
サイクル在庫数 = 1回の発注数(発注ロット数)÷2
例えば、1回の発注数(発注ロット数)が300個であれば、サイクル在庫数 は、150個です。
(計算式:300÷2=150個)
発注頻度が高く、一度の発注量が少なければサイクル在庫は少なくなり、発注頻度が低く、一度の発注量が多ければサイクル在庫は多くなるため、発注ロット数を適正値にすることが重要なポイントです。
適正発注ロット数を決める方法のひとつに経済的発注量(EOQ)があります。
経済的発注量(EOQ)
経済的発注量(EOQ)とは、在庫関連費用の総額が最小限になる発注ロット数(1回当たりの発注量)のことです。
発注に手間がかかり、かつ保管コストのかかる商品に有効な適正在庫の設定方法です。
在庫関連費用とは、在庫費用+発注費用のことです。
- 在庫費用:倉庫費用や光熱費など、在庫を維持するために必要な費用
- 発注費用:発注時にかかる人件費などの費用
1度に大量に発注すると、発注費用は少なくて済みますが、在庫費用が高くなります。
一方、こまめに発注すると、在庫費用は少なくて済みますが、発注費用が増えます。
経済的発注量(EOQ)の計算式
EOQ=√2DS/H
- D = 必要数(需要数)
- S = 1回の発注コスト
- H = 1単位あたりの年間保管コスト
EOQを活用することで、発注頻度と在庫保管コストのバランスを最適化した適正在庫を算出できます。
リードタイムから適正在庫をから計算する(小売業・卸売業)
発注リードタイムが決まっている場合は、平均需要数から計算することもできます。
適正在庫=リードタイムに基づいた計算値+安全在庫
リードタイムから計算する方法
発注リードタイムが30日、1日の平均販売数が5個の場合、サイクル在庫数は150個です。
(計算式:5×30=150個)
リードタイムから適正在庫をから計算する(製造業)
製造業の場合は、部品と仕掛品の管理も必要なため、仕入以外のリードタイムを考慮する必要があります。
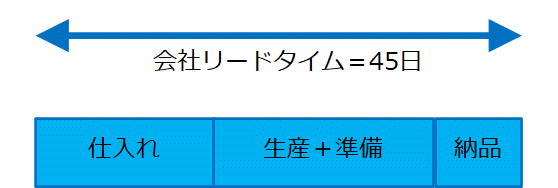
製造業が把握すべき3つの重要なリードタイム
- 仕入れ(発注)リードタイム:材料を発注してから、工場に納品されるまでにかかる日数
- 生産(製造)リードタイム:生産に着手してから、生産完了までにかかる日数
- 納品(出荷)リードタイム:製品を出荷してから客先に届くまでの日数
部品の適正在庫
- 部品の適正在庫数=部品の発注リードタイム×平均使用数+安全在庫数
- 仕掛品の適正在庫数=仕掛品の生産リードタイム×平均使用数+安全在庫数
- 製品の適正在庫数=製品の納品リードタイム×平均出荷数+安全在庫数
製造業の適正在庫の実現・維持する具体的な方法は以下のページで解説しています。
適正在庫の実現・維持のために実践できる5つの方法(製造業限定)
適正在庫を見直して維持するための4つのポイント
適正在庫は一度設定したら終わりではなく、定期的に見直さなければいけません。
ここからは適正在庫を維持するための見直しポイントを解説します。
適正在庫を見直すポイント
- 季節などの周期的な変動
- 商品寿命
- マイナーチェンジやモデルチェンジ
- トラブルや予期せぬ出来事の発生率
季節変動などの周期的な需要変動
代表的な見直しポイントは、季節などの周期的な変動です。
例えば、アイスクリームであれば夏に売れ行きが良く、冬は悪いのが一般的です。
夏と冬の適正在庫が同じであれば、冬は過剰在庫に、夏や欠品続出になります。
つまり、アイスクリームは夏と冬で適正在庫を見直す必要があるということです。
季節変化の影響を受けやすい商材である食品、アパレル、季節家電などは特に注意が必要です。
商品寿命
商品寿命とは、季節などの1年単位の変動ではなく、長期的な売れ行きのトレンドです。
一般的に商品には、次の3つのステージがあります。
- 成長期:販売数が伸びて行っている状態
- 安定期:販売数が安定している状態
- 衰退期:販売数が徐々に減っていって売れゆきが悪くなっている状態
成長期は、どんどん需要が増えるため、在庫数をあまり気にする必要は無く、むしろ需要に合わせて在庫を増やしていくことを考えます。
適正在庫を特に注意したいのは、安定期から衰退期です。
よくあるパターンは、「成長期」と同じ感覚で発注してしまうケースです。
弊社の在庫管理アドバイザーがコンサルティングした会社では、成長期と同じ感覚で発注をし続けた結果、とんでもない量の在庫を抱えてしまっていたケースがありました。
マイナーチェンジやモデルチェンジ
商品寿命は、市場が商品にあきてくると発生する現象ですが、自社のマイナーチェンジやモデルチェンジによって、チェンジ前のモデルの商品寿命が急激に下がってしまうことがあります。
一般的にモデルチェンジやマイナーチェンジのタイミングで旧商品の売れ行きはガタ落ちします。
営業や商品企画、マーケティングの担当者と連携して、商品投入の時期と既存商品の最終仕入れ時期を調整しましょう。
トラブルや予期せぬ出来事がどれだけ起こるかを見積もる
トラブルや予期せぬ出来事への対応では、安全在庫で対応します。
需要の変動以外にも、在庫数の変動要因になるものは様々です。 例えば、
- 仕入れ先の納期遅れ
- 仕入れ品の不良
- 交通渋滞や自然災害
- 納期短縮
- 生産遅れ
- 生産設備のトラブルや不良の発生
- 歩留まりや不良
安全在庫の設定については、次の記事で詳しく解説しています。
需要予測を適正在庫の維持に取り入れる方法と注意点
実施するためには、次の4点が必要です。
- 大量に質の良いデータが必要
- 高度な専門人材
- 部署間連携
需要予測には大量のデータが必要
需要予測は次のように定義されています。
需要予測とは、特定の商品の需要 動向を決める各種の要因とその需要に与える影響を分析し,これをもとに市場調査や 各種の予測結果を考慮して将来の需要を予測すること。
もっと簡単に言えば、「過去に起こったことと全く同じことが起これば、将来も全く同じことが起こる」というのが需要予測の原則的な考え方です。
需要予測をするためには、大量にしかも質の良いデータが必須です。
これが無ければ、需要予測は実施できません。
高度な知識を持った人材が必要
精度の高い需要予測をするためには、膨大なデータと高価なシステムやAI(人工知能)を導入したからといってできるものではありません。
それを使いこなせる高度な人材が必要です。
高度な人材が、膨大なデータの中身を見て、需要予測に適したデータを選定して、需要予測モデルを構築します。
そのモデルはずっと使えるわけでは無く、環境や条件が変わった時に、見極める力も必要です。
例えば、次のようなことが考えられます。
- 定期的な需要変動:アイスクリームの需要
- イベント・行事:お正月、クリスマス、祭り
- 一時的な需要変動:テレビ番組に取り上げられ、一時的に殺到
- 消費税増税:増税前の一時的な消費の盛り上がり
- 販売方法の変更:ネットショップでの販売を始めた
在庫管理の担当者が片手間でやれるような業務ではありません。
部署間連携
高度な人材が一人で奔走しても、需要予測は適正在庫に生かせません。
仮に、正確な需要予測数が出たとしても、発注ロットや生産ロットの都合で、需要予測数通りにならないこともあるでしょう。
各部署が自部門だけの都合を乗り越えて連携し、会社全体で取り組むことが必要です。
【注意】需要予測=適正在庫ではない
「需要予測の計算値=適正在庫」と勘違いしている場合が多いです。
需要予測の計算値は、あくまでも「需要」です。
需要以外に在庫数を変動させる要素はたくさんあります。
適正在庫の実現・維持をサポートするためのシステム・ツール
適正在庫の管理・維持のためには、適切なシステムの導入が不可欠です。以下にいくつかの代表的なシステムとその機能を紹介します。
ERPシステム
ERPシステム(Enterprise Resource Planning)は、企業の経営資源(人材、資材、資金、情報)を統合的に管理するシステムです。
これにより、業務の効率化、情報の一元化、部門間の連携強化を図ることができます。
主な機能には、会計、在庫管理、生産管理、人事管理などが含まれ、リアルタイムでのデータ共有と分析が可能です。
ただし、様々な機能が一元化されている高度なシステムのため、導入費用が高額です。一般的には安くても1000万円~はかかるといわれています。
在庫管理システム
倉庫内の在庫をリアルタイムで追跡し、効率的な在庫管理を実現します。
入出庫管理、棚卸し、ロケーション管理などをサポートします。
在庫管理システムは、ERPシステムに比べると比較的安価なものもそろっており、数千円から利用することができます。
需要予測ソフト
過去の販売データや市場トレンドを分析して将来の需要を予測します。
AIや機械学習を活用することで、予測の精度を高めます。
ただし、需要予測ソフトはデータが大量(少なくとも3年分くらい)にあり、かつ精度が高いことが前提です。
蓄積データが全くない場合は、需要予測ソフトを入れても全く機能しません。
また、先ほど解説した通り、需要予測ソフトを使いこなせる高度な人材も必要です。
在庫管理システムの導入が最優先
中小企業の場合は、まず最初に在庫管理システムを導入することをお勧めします。
在庫管理システムを導入すれば、在庫情報の一元化、リアルタイム化が可能になり、業務効率が上がります。
さらに、データが蓄積できるので、需要予測ソフトの導入も可能になります。
企業規模が大きくなってきたときに、ERPシステムの導入を検討すると良いでしょう。
在庫管理110番が開発した「成長する在庫管理システム」をご紹介します。
今回解説したような適正在庫を維持するための機能を、あなたの会社の事情を考慮してカスタマイズで追加可能です。
実務を知り、数多くの在庫管理の悩みに答えてきた在庫管理の専門家だからこそ実現できる、本当に現場で使える在庫管理システムです。
適正在庫のさらなる低減・安定化を目指す方法(小売業・卸売業)
適正在庫の目標の達成と維持には、現在の業務を見直したり改善することが欠かせません。
適正在庫に大きな影響を持つ3つのポイントは以下の通りです。
適切な発注方法
在庫がある一定量まで減ったら自動的に発注する「定量発注点方式」や、毎週月曜日など定期的に在庫を確認して発注する「定期発注点方式」など、自社の商品特性や発注作業の効率化等、管理体制に合った発注方式を採用し、運用ルールを明確にします。
発注方法は、大きく分けて4つあります。
発注方法の解説は下記の解説記事をご覧ください。
仕入れの改善
仕入れの改善を行うことで、適正在庫を効果的に減らすことが可能です。
仕入先の改善の着目点と管理指標は以下の通りです。
着目点 | 管理指標 | 普段、管理すべきこと |
---|---|---|
発注リードタイム | 納品日数変動率 | 設定した発注リードタイム通りの納品日数か? |
発注ロット数 | 納品数 | 発注ロット数が大きすぎないか?分納ばかりになっていないか? |
納期遅れ | 納期遵守率 | 予定(希望)納期が守られているか? |
不良 | 不良率 | 納入された材料や商品が不良の発生数 |
需要予測精度の向上
需要予測精度を向上させて、発注精度を向上させます。
需要予測精度の向上に必要なのは、次の2点です。
- 十分な量の過去データ(出荷量、販売量データ):少なくとも3年分は必要です
- 予実管理:発注時の予測と実需に発生した実際の現象の検証
上記を使って、売上データを分析し、商品のトレンドや季節変動の見極め、の売れ行きの特徴をつかんで、適正在庫の維持改善に生かします。
需要予測の成功事例として、ぜひご覧いただきたいのがワークマンの取り組みです。
【需要予測の事例】精度を上げるための施策をワークマンから学ぶ
予実管理を行うには、データ分析のスキルが不可欠です。
データ分析と聞くと、難しい専門のソフトが必要と思われがちですが、中小企業のデータ分析はエクセルで十分可能です。
データ分析の具体的な手順や方法は下記の記事で詳しく解説しています。
適正在庫のさらなる低減・安定化を目指す方法(小売業・卸売業)
代替数の製造業は、仕掛品の削減が最も適正在庫の低減・安定化に効果的なので、ぜひ生産効率の向上に取り組みましょう。
生産効率の向上は、生産リードタイムの短縮にも役立ち、納期短縮も実現するため、顧客満足度の向上も期待できます。
生産効率の向上は、次の2つに分かれます。
- 生産能力
- 生産方式
- それ以外
生産能力(生産リードタイムとボトルネック)の適正化
商品を生産する工場には生産能力があります。 原則として単位時間当たりの生産能力を超えて生産をすることはできません。
そこで、生産の前倒しが必要になります。
- 工場の生産能力は1日に50個
- お客からのオーダーが500個(要求納期は4日)
この工場の生産能力では、4日で200個しかつくれません。顧客の要求を守るためには、余分に300個を持っておくのが適正と言えます。
(在庫日数に換算すると6日分の在庫) お客から生産能力を超える注文が続く場合は、次の3つのうちいずれかが必要です。
- 前倒しで見込み生産を行う
- 生産LTを短くする
- 生産能力を増強する
最初は、前倒し生産を行い在庫を積むのが緊急対策になります。しかし、これを行っていると在庫がどんどん積みあがっていくので、本質的な改善として、生産リードタイムを短くしなければいけません。
生産能力の増強(設備導入、人員補強)は最後の手段です。安易に実施してはいけません。
生産リードタイムが伸びてしまう原因は、次のような事です。
- 機械故障:生産能力が落ちてしまう。
- 欠員:生産能力が落ちてしまう。
- 廃棄ロス(歩留り、不良):できる予定の数量ができあがらず、余分に 生産しなければいけなくなる。
- 段取り:生産以外に時間が取られ、予定よりも生産リードタイムが長くなってしまう。
- モノの移動:生産以外に時間が取られ、予定よりも製造リードタイムが長くなってしまう。
- 生産ロット:必要以上に余分に作ってしまう。
- 各種事務処理:処理待ちで生産が止まる。
- ミス:指示数や出来高数が違う。
これらの中で自然に解消するのは欠員くらいで、それ以外の要因は自然に良くなることは無いです。
むしろ放置するとにより拡大する傾向があります。これらはすべて4Mの何らかの不調によるものです。 4Mとは?
生産方式(見込み生産と受注生産)
製造業の場合は、生産方式によって適正在庫の設定が変わります。 生産方式は大きく分けて2つあります。
仕掛品を戦略在庫として持つ(デカップリングポイント)
見込み生産と受注生産の境目のことをデカップリングポイントと言います。
- 受注生産:注文を受けてから生産を開始する
- 見込み生産:注文を見越してあらかじめ生産をして在庫を持つ
受注生産を増やせば在庫は不要ですが、欠品が増えます。一方、見込み生産を増やせば欠品は増えますが、過剰在庫になりやすいです。
適切な生産方式を選ぶことで、欠品を抑えつつ過剰在庫を減らし、しかも納期を短縮することすら可能です。
必ずしも、完全に受注生産や見込み生産である必要はありません。
ある工程の仕掛品までを見込み生産して、その後は受注してから行う・・・という方法でも問題ありません。
デカップリングポイントを活用した最も有名な成功事例は、アメリカのパソコンメーカーのDELLです。(DELLモデルといわれています)
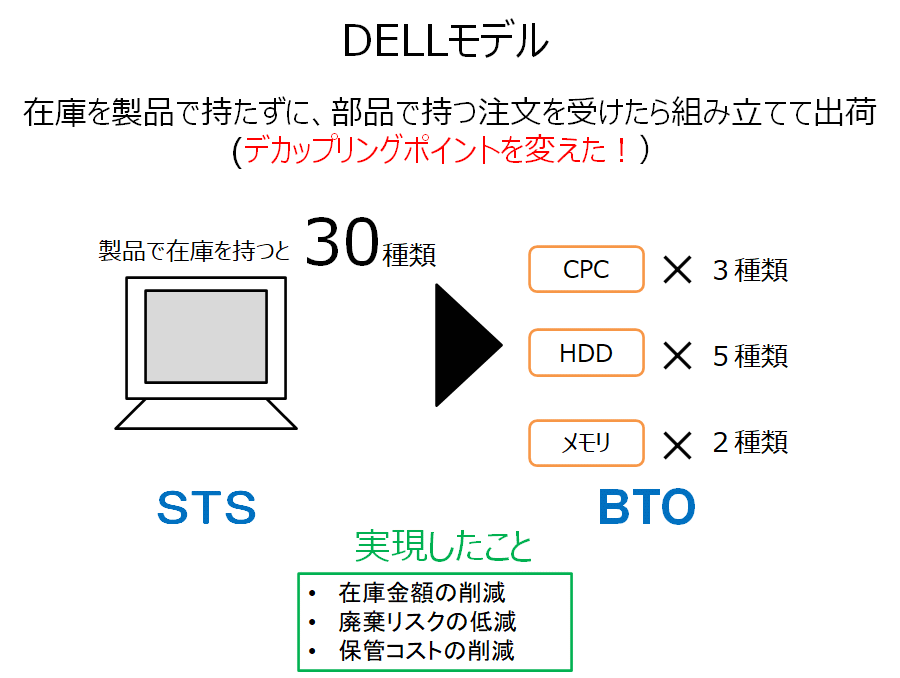
DELLの生産方式の変更
- 従来は、STS:パソコン(完成品)を見込み生産して在庫を持つ。
- 改善後は、BTO:部品在庫を持っておいて、注文を受けてからパソコン組み立てて出荷する
生産方式をSTSからBTOに変えることで、在庫金額を大幅削減しつつ、浮いた管理コストや廃棄コストを製品に還元して低価格化を実現しました。
この手法は、大企業でなくても中小企業でも十分取り組め、かつとても高い効果が見込めます。
デカップリングポイントに関する詳しい解説はこちらをご覧ください。
まとめ
この記事では、「適正在庫」について、以下の点を解説しました。
- 適正在庫とは:欠品による機会損失や、過剰在庫によるコスト増加を防ぐための、最も効率的な在庫量のこと。(安全在庫とは違って、過剰在庫の管理も行うもの)
- 適正在庫の計算方法:経営的観点で、財務視点から売上・在庫回転率などで計算する方法に加えて、実務的観点で、サイクル在庫、やリードタイム、需要予測を考慮して計算できる。
- 適正在庫を維持するポイント:需要予測の精度向上、リードタイムの短縮・最適化、在庫管理ルールの設定と徹底、そして在庫管理システムの活用が鍵となる。
- 適正在庫の維持:一度計算して終わりではなく、季節変動や商品寿命等の市場の変化や状況に合わせて継続的に見直し、改善していく必要があります。
- 適正在庫の低減・安定化:適切な発注方法や予実管理、製造業は生産効率の改善で、さらに在庫金額と無駄なコストを削減し、企業の利益を最大化することが可能です。
まずは自社の在庫状況を正確に把握し、この記事で紹介した計算方法や維持のポイントを参考に、適正在庫の実現に向けた取り組みを始めてみませんか?
自社の適正在庫の計算方法が分かる在庫管理セミナー
適正在庫の重要性は理解できたけれど、「自社だけで実践するのは難しそう」「もっと具体的なノウハウや成功事例を知りたい」と感じていませんか?
そんな方におすすめなのが、在庫管理セミナー「適正在庫と誰にでもできる仕組みづくり」です。
セミナーでは、適正在庫の維持に関するより実践的な知識や、他社の改善事例などを専門家から直接学ぶことができます。自社の在庫管理レベルを一段階引き上げる絶好の機会です。ぜひ、詳細をご確認の上、ご参加ください。
これまで、500名以上が受講した在庫管理110番で一番人気のあるセミナーで、オンラインでも対面でも受講できます。
適正在庫に関するご相談・お問い合わせ
今回の記事を読んで、「自社の状況に合わせた具体的なアドバイスが欲しい」「適正在庫の計算や維持について専門家に相談したい」「在庫管理システムの導入を検討している」など、在庫管理に関するお悩みやご要望がございましたら、お気軽にお問い合わせください。経験豊富な在庫管理アドバイザーが、貴社の課題や状況を丁寧にヒアリングし、最適な解決策をご提案いたします。
適正在庫に関する関連記事