この記事では、実際に在庫管理の現場の改善支援を行っている在庫管理アドバイザーが、適正在庫の実現、維持、さらには注意すべき点までを分かりやすく、かつ具体的に解説します。
- 適正在庫と安全在庫との違い
- 適正在庫の計算方法
- 適正在庫と安全在庫の違い
- 適正在庫の目安と決め方、3つの方法
- 適正在庫を実現&維持するための10の方法
- 適正在庫を維持するためにやっておくべき3つのこと
- 特に注意すべき適正在庫の維持に考慮すべき3つの需要特性
在庫管理110番では、適正在庫の考え方、具体的な計算方法から発注方法の選び方など、適正在庫に必要な事が学べる在庫管理セミナーを実施中です。これまで300名以上が受講した人気のセミナーです。
具体的な適正在庫の計算方法、維持するコツなどを在庫管理アドバイザーから学べます。
受講者限定の特典あります!
目次
適正在庫の考え方と安全在庫との違い
勘違いされやすいのが、安全在庫と適正在庫です。
安全在庫とは、欠品を防ぐためだけの下限在庫数です。適正在庫とは、欠品を防ぐためだけではなく、過剰在庫を防ぐため、在庫数の上限を設定します。
適正在庫が維持ができている状態=在庫上限数と在庫下減数の間にある状態です。
とはいえ、安全在庫も重要です。安全在庫の計算方法や適正在庫と安全在庫の違いを詳しく解説した記事をご紹介します。
適正在庫の計算方法
それでは、在庫管理の具体的な計算方法を3つ解説します。
在庫回転率
在庫回転率を使って、適正在庫を計算可能です。
在庫回転率の計算式は、以下の通りです。
上記の指揮を見ると分かるように、在庫回転率が分かれば、目標の在庫金額(=適正在庫金額)を計算することが可能です。
在庫回転率を使った適正在庫の計算方法と具体的な活用法はこちら
在庫回転率は、在庫の流動性を計る指標です。
つまり、在庫回転率が良ければ、流動性が高い(=在庫が素早くお金に替わっている)ことを示しているため、キャッシュフローが良い状態になります。
交叉比率
交叉比率とは、本当に在庫が儲かっているかどうかを見る指標です。
在庫回転率に粗利率を加えて計算したもので計算式は、交叉比率=粗利率×在庫回転率です。
在庫回転率だと、単に在庫の流動性だけしか分かりませんが、交叉比率の場合は、粗利も一緒に見ることができます。
交叉比率を使って粗利目標を立てつつ、在庫回転率の目標を達成するということも可能です。
例えば、下記のグラフは交叉比率200を達成するときに必要な粗利率と在庫回転率(在庫回転日数)の関係を表したものです。
適正在庫の決め方と目安、3つの方法
それでは適正在庫の目安とはどれくらいでしょうか?
適正在庫の決め方は、経営的観点と実務的観点から決める方法があります。
経営的観点から適正在庫を決める
経営的観点から適正在庫を決める場合は、財務的な在庫金額が適正在庫になります。
決める方法はいくつかありますが、代表的な方法は以下の通りです。
売上目標値から決める
売上目標値から、在庫金額を決めます。
一般的に売上金額の多くても10%以下が、適正な在庫金額といえます。
例えば、売上が1億円の企業であれば、目標とする在庫金額は、1000万円以下です。
資金繰りからから決める
資金繰りを管理する指標であるキャッシュコンバージョンサイクル(CCC、Cash Conversion Cycle)から計算できます。
CCCとは、企業が商品や原材料を仕入れてから販売し、さらに現金化するまでの日数を計る指標です。を受け取るまでの時間を測る指標です。
例えば、CCCが90日の場合、仕入れに使った1000円が手元に戻ってくるまでに90日かかるいうことです。CCCは短ければ短いほうが良いです。
CCCの計算方法式は以下の通りです。
CCC= 在庫回転日数+売掛債権回転日数-買掛債務回転日数(DPO)
- 売掛債権回転日数:売り上げを回収するのにかかる時間(入金サイト)
- 買掛債務回転日数:支払い期限(支払いサイト)
仮に、CCCの目標値を40日、売掛債権回転日数が120日、買掛債務回転日数が60日の場合、
目標となる在庫回転日数は10日となります。
在庫回転日数=CCC(60日)-売掛債権回転日数(90日)+買掛債務回転日数(40日)
在庫回転日数が分かれば、適正在庫金額の設定は可能です。
在庫回転率を使った適正在庫の計算方法と具体的な活用法はこちら
実務的観点から適正在庫を決める
実務的観点から適正在庫を決める方法は主に2つあります。
リードタイムから算出する
主なリードタイムは、次の3種類です。
- 発注LT(部品や商品を発注してから、納品されるまでの日数)
- 製造LT(製品の生産着手から完成までの日数)※製造業のみ
- 納品LT(商品や製品をお客様に届けるまでの日数)
例えば、商品Aの発注リードタイムが7日の場合、商品Aの必要在庫数は7日分です。
商品Aが1日に平均10個売れる場合は、7×10=70個となり、これが適正在庫数です。
ロット数や最低発注数(MOQ)算出する
ロット数とは「1回当たりの発注単位」で、最低発注数とは、購入者が発注しなければいけない最小数量です。
ロット数や最低発注数は適正在庫となるのは、ロット数や最低発注数が、発注LT×必要数量を超えている場合のみです。
経営的観点と実務的観点から適正在庫を計算するための具体的な方法は、下記の記事でとても詳しく解説しています。
競合との比較や業界標準から決める
最後に競合や業界標準から決める方法です。
取り扱う商材や業界、または業績の良い競合他社をベンチマークにして適正在庫金額を決めることもできます。
例えば、製造業の場合だと、39.3~49.9が目安です。
ただし、ご覧いただくと分かるように、生産品目で、若干違いがあります。
適正在庫を実現・維持する10の方法
適正在庫を達成して、維持する10の方法をお伝えします。
書いてある順番=取り組み優先度と効果の出しやすい方法です。
適正在庫=需要予測と思われがちです。
しかし、大多数の企業は需要予測をするレベルに全く至っていないのが現状です。
上から順番に見て、できていないことを実施していきましょう。
過剰・滞留・不良在庫の整理
現場が在庫にあふれていて、過剰・滞留・不良在庫が既に多い場合は、最初に整理を実施しましょう。
そもそも整理をしなければ、必要なものが、あふれて見つからなくなったり、後述する保管場所の整頓も不可能です。
整理の方法としては、赤札作戦がおすすめです。
在庫精度を高める
在庫精度の低い会社は、欠品も過剰在庫も多いです。
少なくとも在庫精度=95%(在庫差異率5%以下)を目指しましょう。
在庫精度が悪いと、在庫があるかどうかが不安という心理が働くので、発注量も生産量も増える傾向にあります。
在庫精度が高いだけで、「不安」が無くなるため、発注量や生産数を減らせます。
そもそも在庫精度がわからない会社は残念ながら論外です。
棚卸を実施して自社の在庫精度を正しく把握しましょう。
保管場所の見直し(整頓の実施)
在庫の保管が乱雑だと、置いてある場所がわからず紛失が増えます。
結果的に、あるはずのものが無かったり、無いと思っていたものがあったりと、欠品も過剰在庫も増えます。
在庫の保管場所を特定の人の記憶に頼っている場合も要注意です。
特に忙しい場合には、記憶が曖昧になりがちです。
新人でもパートさんでも置き場を作りましょう。
発注残管理をする
発注残管理とは、発注したものを記録することです。
発注管理をすることで、二重発注(発注しているにもかかわらず、発注をしてしまうこと)や発注漏れを防ぎます。
失敗しない発注管理のポイントは以下の点です。
- 一元管理する。(個人のエクセルで個々に管理しない)
- 発注数だけではなく、納品数(未納数)も管理する。
- 回答納期を取る
引当管理をする
引当在庫(予約在庫)管理とは、顧客の注文や将来の生産予定に対して予め在庫を確保することです。倉庫に保管している在庫をあらかじめ特定の顧客注文や生産計画に割り当てる(引き当てる)在庫のことを指します。
引当在庫管理を実施していないと、他のお客の注文を誤って別のお客様に販売してしまったり、注文が入っていることに気づかず、発注が遅れ欠品します。
先々の予定された販売や生産にな在庫を確保しトラブルなくスムーズに進めることができます。
引当在庫数の計算式は次の通りです。
引当在庫数=総在庫数−フリー在庫数
- 倉庫在庫数: 倉庫に物理的に存在する総在庫数。
- フリー在庫数: まだどの注文にも割り当てられていない、自由に利用可能な在庫数。
- 引当在庫数: 既に特定の注文や用途に割り当てられ、他の目的には利用できない在庫数。
発注方式を見直す
適切な発注方式を選択することで、適正在庫だけではなく作業効率にも効果的です。
適正在庫の維持できる2つの理由
- 在庫過剰と欠品のリスク低減:
適切な発注方式を選択することで、在庫過剰や欠品のリスクを効果的に管理できます。
たとえば、発注点発注の導入で、発注漏れを防げます。需要予測に基づく発注システムを使用することで、実際の需要パターンに合わせて在庫レベルを調整し、過剰な在庫を抱えることなく、また、需要のピーク時に欠品を未然に防げます。 - キャッシュフローの改善:
適切な発注方式により、必要な在庫を適切なタイミングで発注できます。これにより、不必要な在庫を持たずに済むので在庫回転率が良くなるためキャッシュフローが改善します。
- 在庫過剰と欠品のリスク低減:
作業効率が良くなる理由
- 発注業務の省力化・自動化:
最適な発注方式を選択することで、発注作業を自動化(省力化)できます。手動で発注するものを見つけて発注する作業を減らせます。例えば、発注点発注を導入すれば、在庫数がある特定数量に達した時に自動的に発注が行われるように設定できます。これにより、手作業による注文プロセスのミスを減らし、作業効率を大幅に向上させることができます。 - ベテランに頼らず初心者でも発注できる:
適切な発注方式を採用することで、発注を熟知したベテランでなくても初心者でも発注できるようになります。在庫管理が上手に回っている会社は、「発注業務はパートやアルバイトの仕事で、社員の仕事では無い」と口をそろえて言います。私もその意見は賛成です。これにより、従業員はより価値の高い活動に集中することが可能になり、企業のリソースを最大限に活用できます。
- 発注業務の省力化・自動化:
4つの発注方法
発注方法は、次の4つに分けることができます。
発注方式は、発注する時期(定期、不定期)と、発注数(定量、不定量)の組み合わせで、4つに分類できます。(1~4の順番で難易度が上がる)
- 定期・定量発注:決まった時期に、決まった数量を発注する方法。もっとも簡単
- 不定期・定量発注:在庫がある数量を下回った時に、決まった数量を発注する(いわゆる発注点発注)
- 定期・不定量発注:決まった時期に必要な数量の発注を行うことです。(いわゆるMRP発注)
- 不定期・不定量発注:必要な時に、必要な数量を発注する方法です。(一番難易度が高い)
商品の特性によっては、発注方法が必然的に決まる場合があります。
例えば、船便で運ぶ輸入品などは、「定期・定量発注」または、「定期・不定量発注」しか選択できません。
各発注方法の特徴と選び方は、以下の記事をご覧ください。
仕入先管理
仕入先管理ができていないと、入ってくる日がわからないため、余分な在庫を持たなければいけません。
仕入先管理も適正在庫のために欠かせません。
在庫管理ができている会社は、例外なく仕入先管理がキチンとできています。
仕入先管理のポイントは以下の3点です。
- 回答納期を取る:こちらの要望する納期を守れるかどうか
- 納期遵守率:決まった納期を守ってもらう
- 発注リードタイムの取り決め:標準発注LTが決まっており、安定している
仕入先が原因で、適正在庫が達成・維持できないということは私たちの支援先でもよくあります。
交渉したいのは、実施したいのは以下の2点です。
- リードタイムの短縮(発注LTを短くする)
- ロット数や最低発注量(MOQ)の見直し
仮に単価が少し上がったとしても、リードタイムの短縮やロット数の変更がメリットになることはよくあることです。
失敗例として、私の支援先が、単価が下がるということだけを理由に、国内調達していた部品を海外調達(輸入品)に切り替えたことがありました。
その結果、これまで発注リードタイムが7日(必要な在庫は7日分)だったのに、海外調達に切り替えることで、発注リードタイムが40日になり、さらに最低発注数が1コンテナ分になり、キャッシュフローが
急激に悪化しました。さらに、保管場所も拡張せざるを得なくなり、保管費用も上昇しました。
調達先の切り替え
納期が守れない、ロット数が多すぎる、品質不良が多い、といったような仕入先の場合は、あなたの会社にとって大きなリスクです。
たとえ、古い付き合いがあったとしても、切り替えを検討すべきでしょう。
ただし、あなたが下請法にかかるような規模の場合は要注意です。
具体的には、資本金が1000万円を超えると、たとえ中小企業であっても下請法に抵触する可能性があります。
在庫の持ち方にメリハリをつける
商品の適正在庫は一度設定したらずっと同じではありません。
(季節性の高い商品(アイスクリーム等)などが該当します。)
例えば、下記のグラフのように、販売数が周期的に変動している商品があったとします。
1月の販売数がピークで、3月~4月にかけての販売数は60%以上もダウンしています。
1月を基準にして、発注点や安全在庫を設定すると過剰在庫になりキャッシュフローも悪化します。
11月を基準にして、発注点や安全在庫を設定すると、欠品が多発し、売上機会の損失につながります。
必要な時には在庫数を多く確保し、不要な時期には在庫数を減らすのが適正在庫です。
部品表やセット品管理を取り入れる
部品表とは、製品を構成している部品や原材料をまとめたものです。(製造業の方はなじみがあると思います。)
セット品とはお歳暮など、複数の商品や付属品を組み合わせて1つの商品として販売するものです。料理でいえば、レシピです。
注文がきたらすぐに販売できるように、製品やセット品を作り置きすることはよくあると思います。
そんな時に、部品表やセット品管理ができていると便利です。
セット品管理ができている場合
お歳暮を2セット作った場合。
お歳暮を2セットの在庫を計上したと同時に、ビール12缶、ハム2本、ゼリー6個、チーズ3個の在庫が引き落としされる。
という在庫管理ができます。
セット品管理ができていない場合
お歳暮を2セットを作ったとしても、お歳暮が2セットあるかどうかがわからず、ビール12缶、ハム2本、ゼリー6個、チーズ3個がお歳暮用に使われているかどうかすらわかりません。
お歳暮の準備数が足りなくなって、売上機会の損失、ビール、ハム、ゼリー、チーズが減っていることに気づかず、発注漏れ。
といったことが起こり、足りなくならないように余分に在庫を持ちすぎる過剰在庫や、作り置き数不足や材料不足による欠品が起こります。
部品表とセット品は、適正在庫だけではなく、原価管理にも役立ちます。下記の記事で詳しく解説しています。
また、適正在庫と発注の効率化に役立つMRP(自動発注の仕組みのひとつ)を実施する場合、部品表の考え方の理解は必須です。
需要予測
需要予測とは、過去のデータ分析、市場のトレンド、季節性、経済状況など多様な要因を考慮して、将来の必要数を予測する方法です。
適切な需要予測によって、将来の需要数が読めるようになるので、製品の需要の増減を見据えて、発注数を調整可能です。
需要予測は、適正在庫を実現&維持するうえで強力な方法ですが、注意点も多いです。
下記の注意点が一つでも欠けていると、正しい需要予測ができません。
需要予測を実施する際の注意点
- データの正確性:予測の精度は、使用するデータの質と量に大きく依存します。不正確または不完全なデータだと、誤った予測結果になります。
- 複数の予測手法の活用:一つの予測手法が万能ではありません。一つの依存するのではなく、複数の予測手法を組み合わせることで、より正確な需要予測ができます。
- 影響を与える要因の考慮:過去の販売数だけでは、需要予測はできません。経済状況、競合他社の動向、季節性など、外部環境の変化が需要に影響を与えているかもしれないので、これらの要因を考慮する必要があります。
- 継続的な見直し:社会情勢や市場の状況は常に変化するため、定期的に需要予測や手法の見直し・調整が必要です。ずっと同じ方法は通用しません。
- 内部コミュニケーション:いくら正確な需要予測ができたとしても、それに対応できる組織体制や生産体制でなければ意味がありません。需要予測の結果を生産、販売、在庫管理などの関連部門と共有し、組織全体で対応策を調整することが必要です。
製造業の適正在庫の目指し方・維持する方法
製造業は、生産というプロセスがあるため、他の業種と同じ方法だけでは適正在庫は維持できません。
製造業の適正在庫の実現・維持の方法は、別の記事でまとめています。
適正在庫を維持するために絶対にやるべき3つのこと
適正在庫は、特定の経験や勘だけでは維持できません。
適正在庫を維持するためには、在庫データの活用が不可欠です。
ここでは、在庫データを活用して、適正在庫を維持する3つの方法を解説します。
在庫管理システムの導入
エクセルだけでは難しく、在庫管理システムの導入は、適正在庫を維持には必須です。
在庫管理システムの主な役割は次の4点です。
- データの蓄積:後述する在庫分析に必要なデータを蓄積します。
- アラート:発注点等の設定をしておけば、発注点に達したときにメールなどで知らせてくれるので気づきます。
- 効率化:複雑な作業や計算をシステムがやってくれます。
- 一元管理:情報を全員で共有できるため欠品や過剰在庫を予防できます。
また、在庫管理システムの導入は、業務の標準化の推進、属人化予防にも効果的です。
在庫分析の実施
在庫管理システムで収集した在庫データを分析します。
在庫分析の目的は、今、設定している適正在庫水準が適正かどうかを見るためです。
在庫分析は、エクセルで十分です。エクセルのほうがデータが使いやすく、様々な角度から分析しやすいです。
在庫分析でまず取り組んでいただきたいのが、ABC分析です。
在庫金額や在庫回転率でABC分析を行い、在庫の状態(改善に着手する優先度等)を調べることができます。
また、エくセルだけで、次のようなグラフや集計表をほぼ自動で作れます。
マクロや複雑な関数を使わなくても、便利な機能がたくさんあります。
在庫分析の自動化、省力化をするために、在庫管理110番のおすすめは、次の2点です。(リンク先は、サンプルファイル付きの解説です)
システムに蓄積したデータをエクセルを使って分析してみましょう。きっと、気づかなかった事、思い込みに気づき、適正在庫の見直しと維持に役立つでしょう。
定期的な在庫監視(棚卸の実施)
棚卸を定期的に実施しましょう。
特に在庫精度が95%を切っているような会社は、毎月または3カ月に1回することをお勧めします。
適正在庫を維持する方法で、最初に挙げたように在庫精度は、最も大切な要素です。
また、棚卸をすれば、必然的に現場を隅々まで見ることになるので、現場の状態(特に整理・整頓)のチェックにもつながります。
棚卸の精度が低い、時間がかかりすぎているというお悩みがありましたら、こちらをご覧ください。
在庫の精度向上と時間短縮は両立可能です。
適正在庫の維持に特に注意すべき3つの需要特性
特に、適正在庫を維持するにあたって、以下のような特性のある商品を扱っている場合は、注意が必要です。
季節性など周期的な需要変動がある商品
季節変動のように、需要が周期的変動するような商品は、直近過去の平均値を使ってはいけません。
具体的な計算例は下記の通りです。
ご覧いただくと分かるように、過去3か月分のデータで、需要数を計算すると、400個も欠品してしまいます。
一方、過去の同時期で計算した場合の誤差はわずか15個です。
需要に周期性のある商品の場合は、過去の同時期を使って需要数を計算します。
イベント需要が高い商品
節分、ハロウィン、クリスマスなど特定の時期だけ需要が急増または需要のある商材は、そのスポット時のみ在庫を積み増します。
また、イベントが終わったら、急激に需要が減少するため、早期に売り尽くし等を行い在庫が残らないようにします。
商品寿命が短い商品
商品寿命の短さは、品質的な商品寿命と社会的な商品寿命があります。
- 品質的な商品寿命:消費期限(食品)や錆(鉄製品)、メーカーが定めた使用期限(バッテリー等)など
売れ残りが、即廃棄につながる可能性が高いため、仕入れすぎに注意します。 - 社会的な商品寿命:流行に左右されやすい商品(アパレル)や決まった時期を過ぎると売れなくなるもの(カレンダー等)
流行が過ぎると一気に売れなくなります。売れている途中の再仕入れをどこで止めるかが重要です。最近の事例では、新型コロナウイルス対策のマスクや消毒液がこのようなものに該当します。
まとめ
適正在庫のメリットから計算方法、さらには具体的な実現方法から注意点までをお伝えしました。
簡単にまとめると、次の4点です。
- 適正在庫にメリットはあってもデメリットは無い。(財務、顧客満足、生産性向上、会社にとっても従業員にとってもメリットあり)
- 適正在庫を実現する方法は需要予測だけではない。むしろ他にもっと確実で効果を出しやすい方法がある。
- 適正在庫を実現・維持するためには、在庫管理システムの導入は必須。エクセルだけでは難しい。
- 季節性のある商品、イベント需要の高い商品、商品寿命が短い商品は特に管理に注意。
よくある適正在庫の質問(1問1問)
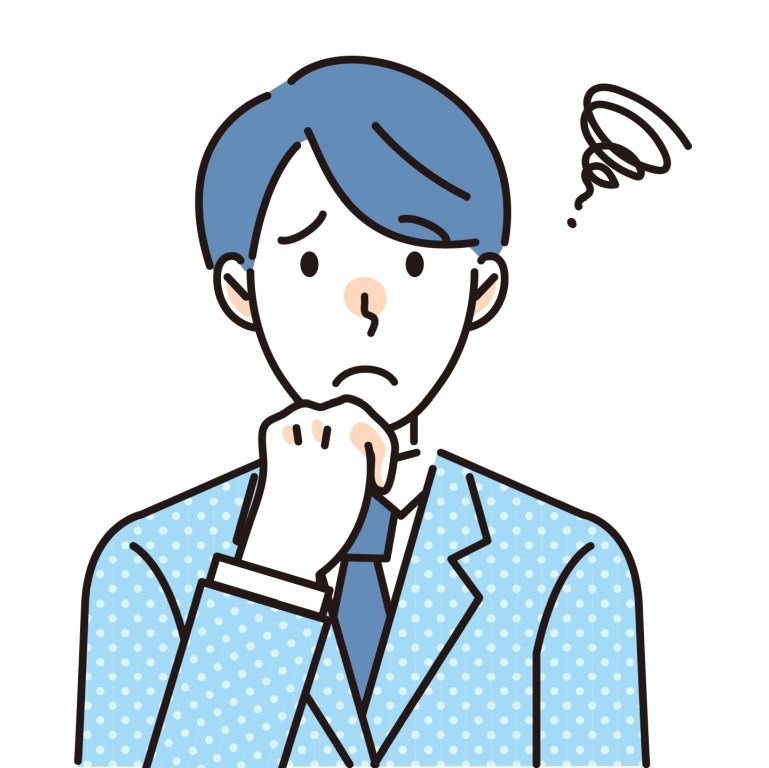
発注(または生産)する際のロット数が決まっている場合の一般的な考え方についてご教授頂けないでしょうか?
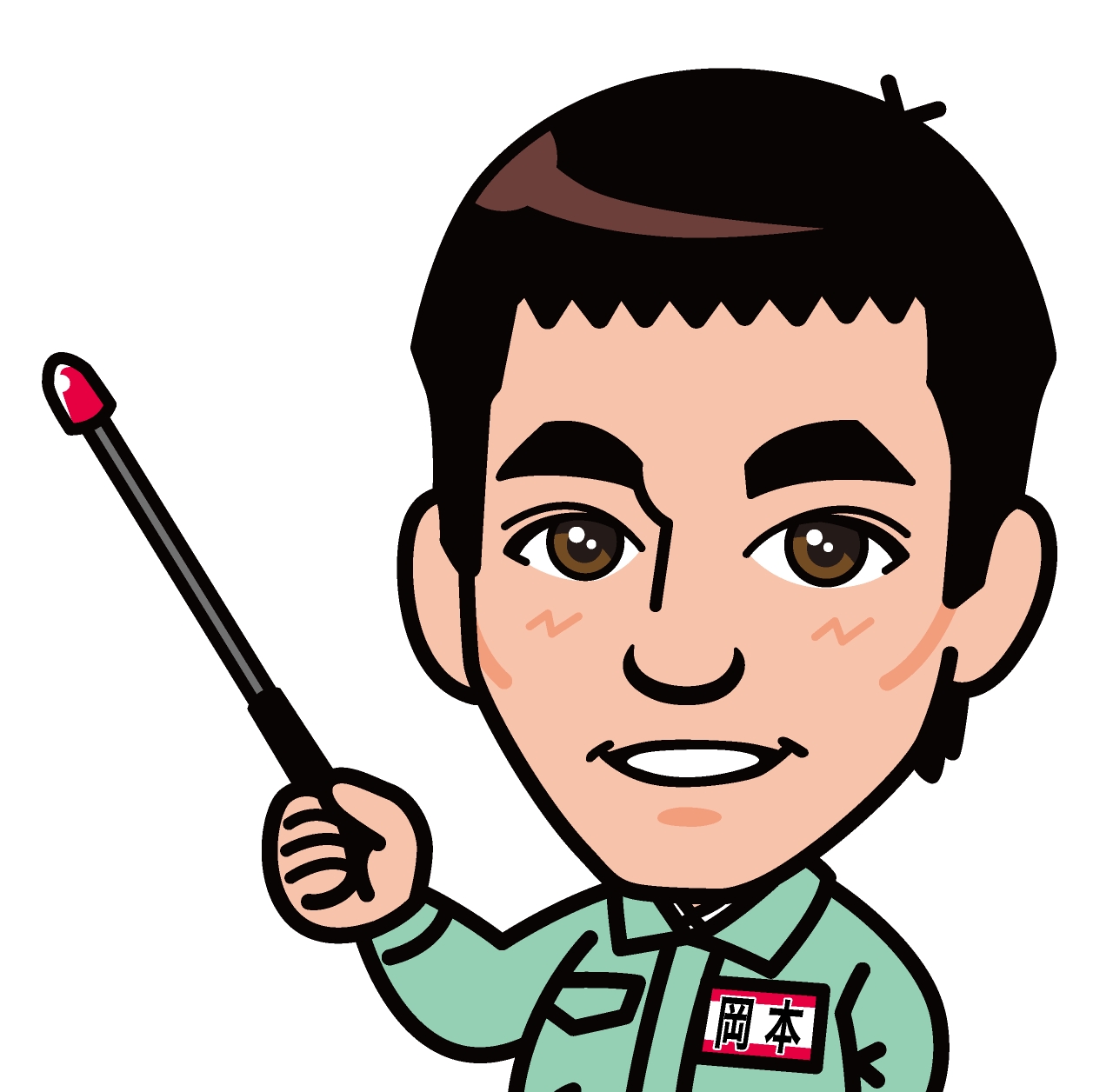
決まっているロット数を在庫回転日数に置き換えて計算してください。
これが適正在庫の範囲内であれば問題無いですが、適正在庫の範囲を超えている場合は、見直しが必要です。
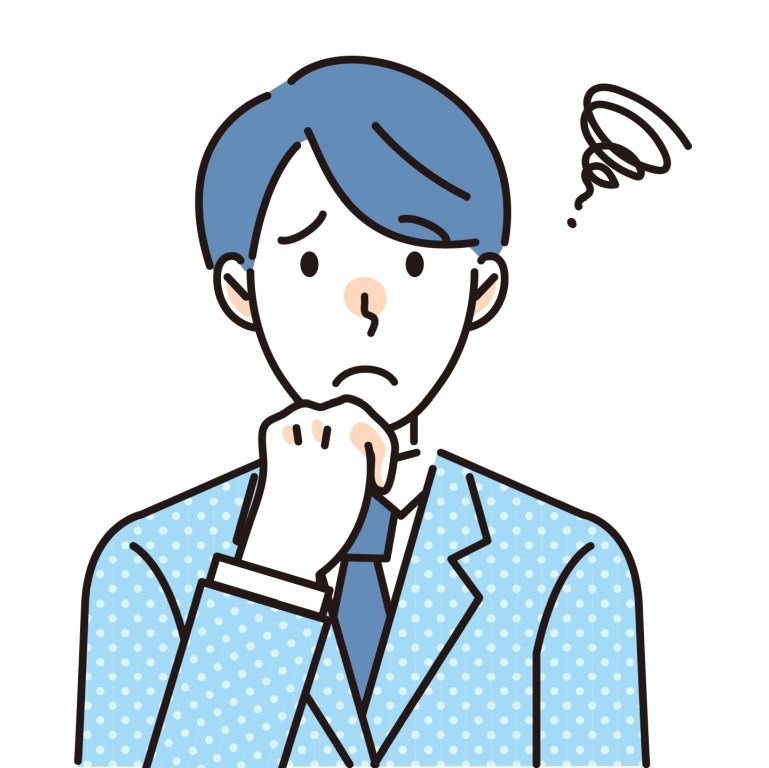
一度設定した「発注点」はいつ、どのように見直せば良いのでしょうか?
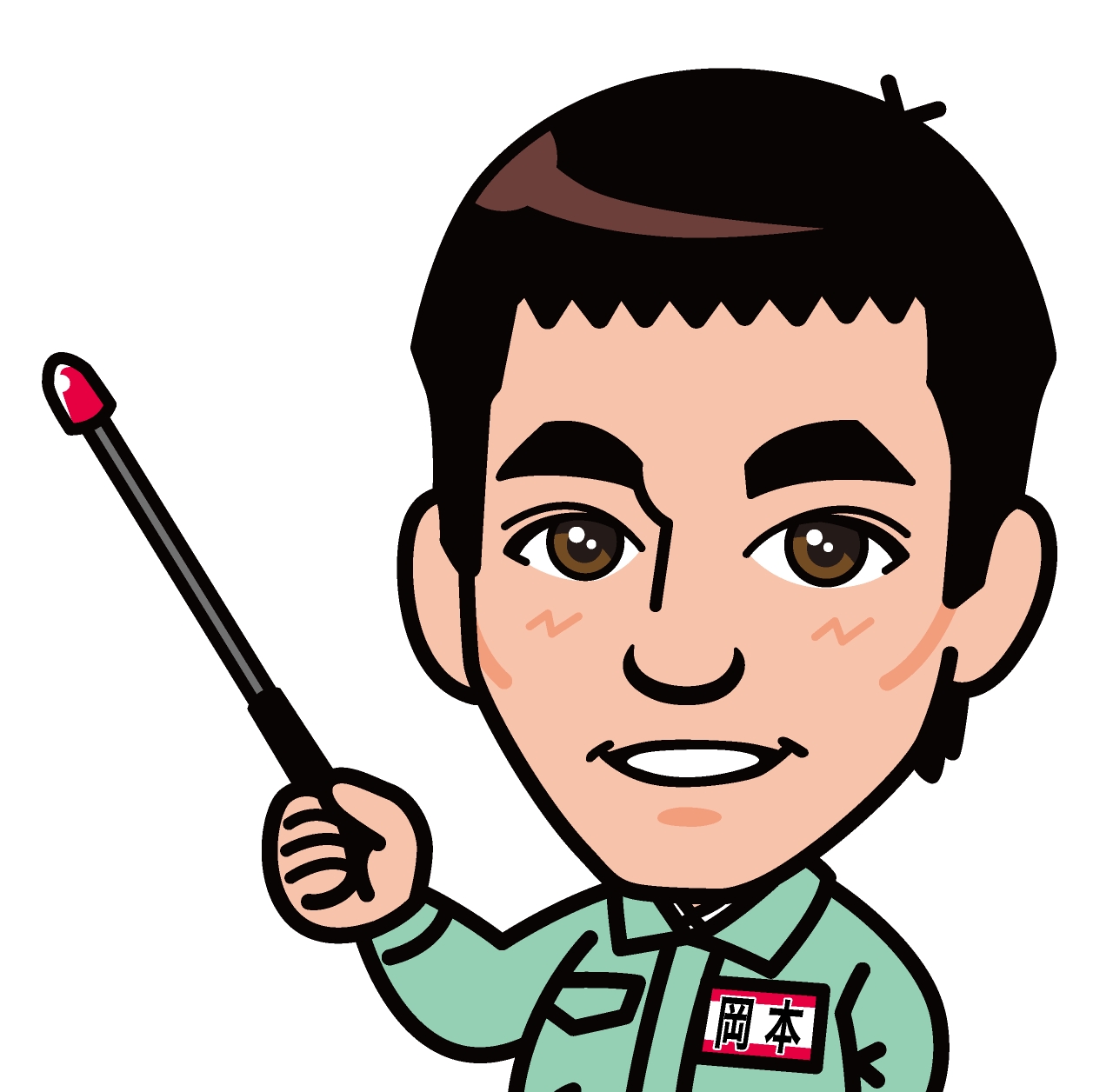
手動で毎回やるのは大変ですが、システム化すればそんなに難しくはありません。
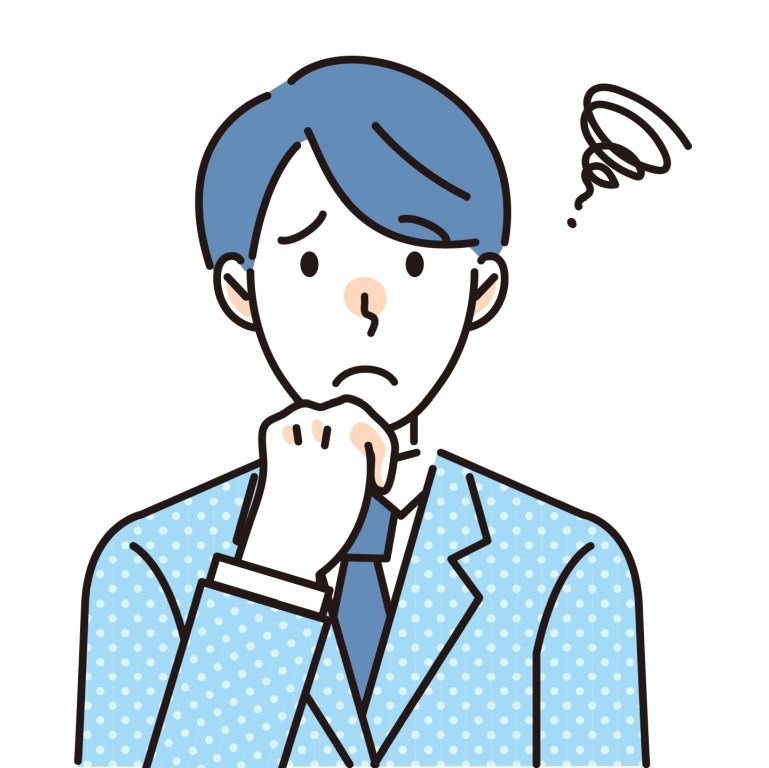
会社から適正在庫の目標値が示されず、とにかく在庫を減らせ!と指示を受けます。どうすれば良いでしょうか?
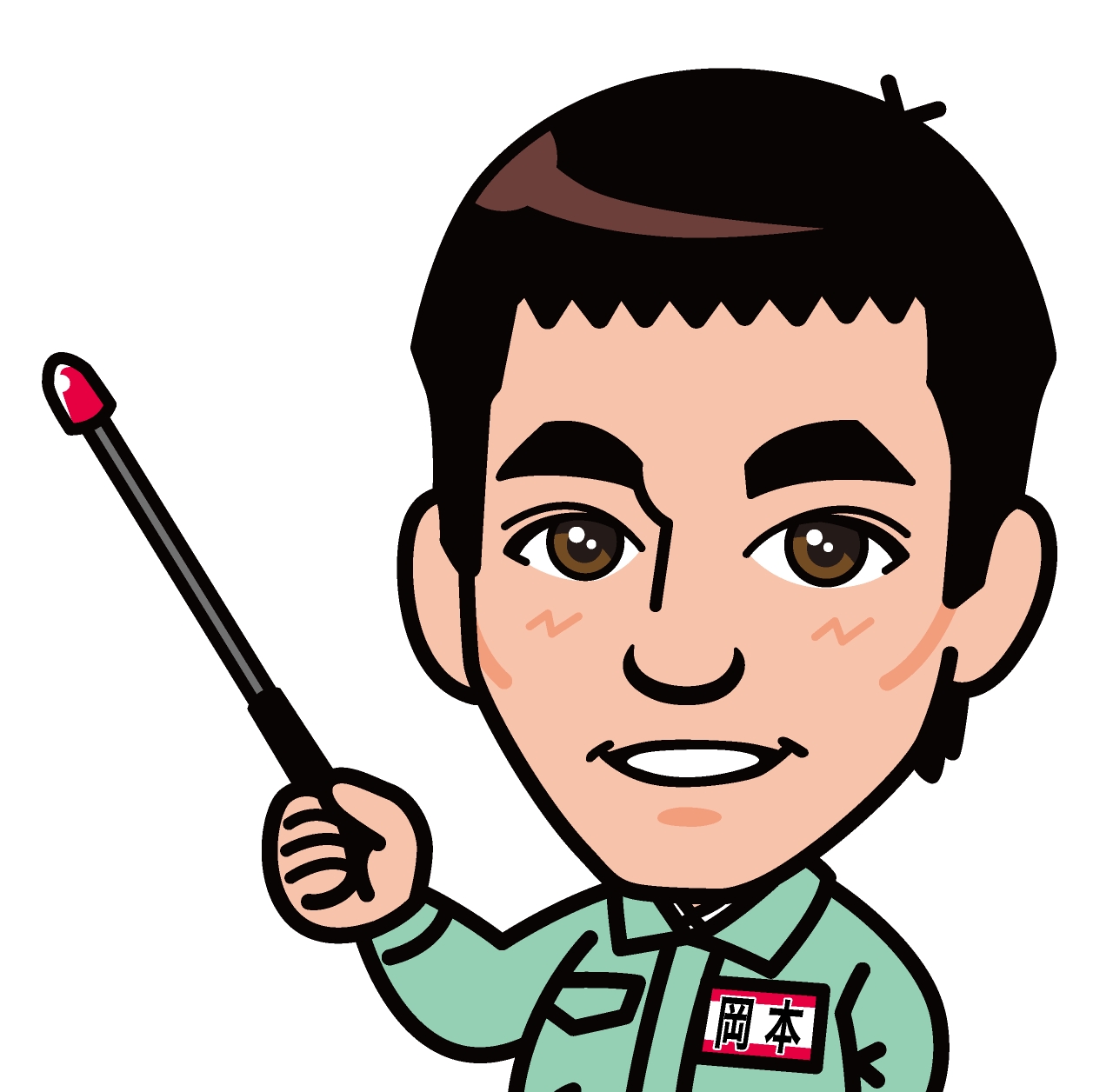
現在の状況にもよりますが、20~30%削減を目標値としてみてはいかがでしょうか?
基準値が無いと、目標値が定まらないのでとにかく設定してみるのがおすすめです。
適正在庫の考え方を学ぶ
在庫管理110番では、適正在庫の考え方、具体的な計算方法から発注方法の選び方など、適正在庫に必要な事が学べる在庫管理セミナーを実施中です。これまで300名以上が受講した人気のセミナーです。
受講者限定の特典をご用意しています
在庫管理システム
そもそもデータを収集する仕組みが無いという場合は、在庫管理システムの導入をお勧めします。
データが活用できるように、データを簡単にエクセルに落とせる仕組みを標準搭載しています。
また、成長する在庫管理システムのコンセプトは使い切れるシステムです。
導入した機能を100%使える状態にすることで、役立つことはもちろんのこと、自社に必要な機能だけなので、シンプルで誰でも使え、低コストを実現できます。
実務を経験したものとして、そして在庫管理の専門家として、不満を解消するために作った在庫管理システムです。
成長する在庫管理システムの特徴や詳しい機能はこちらからご覧ください。
低コストで自社に必要な機能を持ったシステムが導入できる
在庫管理のご相談、お問い合わせ
在庫管理110番では、適正在庫に関するご相談を随時受付中です。
無料個別相談も実施中ですので、今回の記事で分からなかったこと、自社はどのようにすれば良いかイマイチ理解できなかったことなど、お気軽に在庫管理アドバイザーにご相談できます。
自社の状況、事例に合わせたアドバイスがもらえます。
些細なことでも遠慮なくご相談ください!